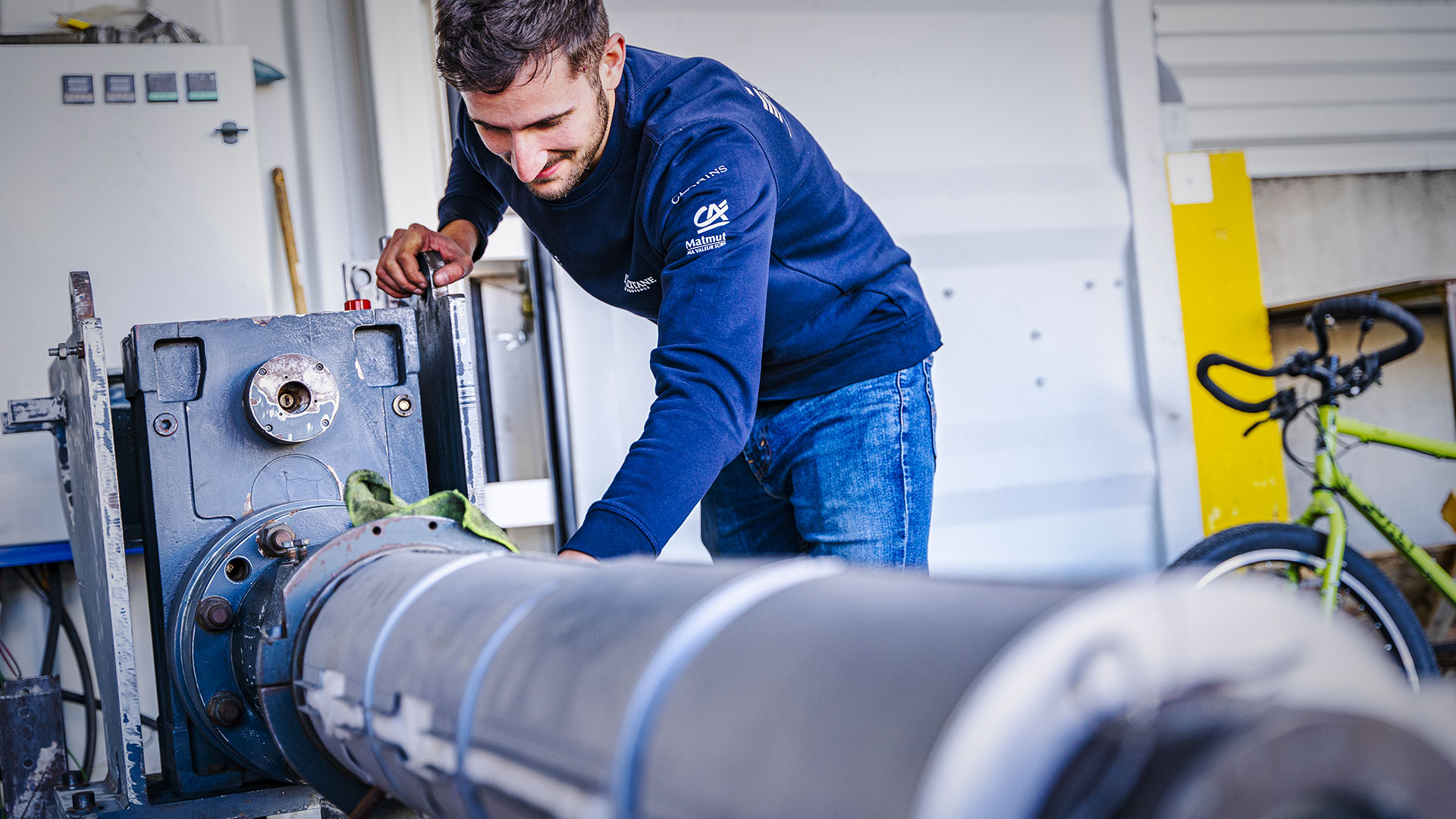
Article rédigé par Tom Bébien, Responsable de l’atelier de recyclage de Plastic Odyssey.
Le rôle des machines de recyclage
L’utilisation des ces machines à bord servira à effectuer des démonstrations pour convaincre les entrepreneurs des pays d’escale de les reproduire et de les installer à terre. Leur rôle est simple : montrer que les déchets plastiques peuvent être des ressources. Lorsqu’il est collecté et transformé, le plastique peut répondre à un besoin très local : construction de structures, irrigation pour l’agriculture, création de sol et de mobilier, etc.
Cette semaine, on vous emmène dans les coulisses de notre atelier de valorisation des déchets plastiques. De la conception à leur fabrication, vous saurez tout sur notre démarche de développement technique.
Mise à jour du mardi 16 mars 2021
Des machines simples, adaptables et open-source
Ces machines ont été élaborées en prenant en compte trois critères primordiaux :
- L’aspect low-tech : elles sont construites avec des matériaux de bases que l’on retrouve partout. Elles sont constructibles et réparables avec de l’outillage simple.
- L’adaptation : la conception des machines n’est pas unique, nous sommes partis d’un principe de base efficace et nous pouvons adapter la géométrie, l’échelle, et l’alimentation en fonction des situations.
- Leur conception et fabrication sont libres de droit : en élaborant nos propres machines, nous avons la main sur l’ensemble de la construction et nous connaissons les pièces dans les moindres détails. Nous pouvons ainsi diffuser et partager tous les éléments et les améliorer en collaboration avec les acteurs locaux
La démarche de l’atelier de valorisation
Le principe de notre démarche est d’avoir une première base de machines efficaces pour pouvoir les faire évoluer. Nous ciblons ensuite les zones dépourvues de moyens de gestion dans lesquelles les déchets plastiques s’accumulent. Enfin, nous travaillons avec des acteurs locaux pour adapter ces machines à un usage défini afin de donner une seconde vie aux déchets existants sur place.
De quoi est composé l’atelier de valorisation des déchets plastiques ?
Aujourd’hui, nous avons un atelier composé de trois parties :
- La partie « préparation de la matière » qui comprend un broyeur, un bac de lavage et une centrifugeuse pour broyer, laver et sécher les déchets plastiques.
- La partie « transformation » qui nous permet de re-former la matière grâce à une extrudeuse et des moules de tailles et formes diverses, ou encore grâce à un four et une presse hydraulique.
- La partie « valorisation énergétique » qui nous permet, grâce à la pyrolyse, de valoriser une partie des déchets plastiques qui ne sont plus ou pas recyclables en carburant.
Au total, nous disposons de 10 machines : 7 que nous avons conçues et fabriquées, d’1 machine que nous avons récupéré et adapté à nos besoins et de 2 autres machines achetées (car très basiques).
Les machines sont aujourd’hui peaufinées à Marseille pour s’adapter au navire, puis elles seront envoyées à Dunkerque et embarquées à bord courant avril. Une fois installées, ces machines pourront alors être testées en condition réelle ce qui lancera officiellement le début de notre expédition !
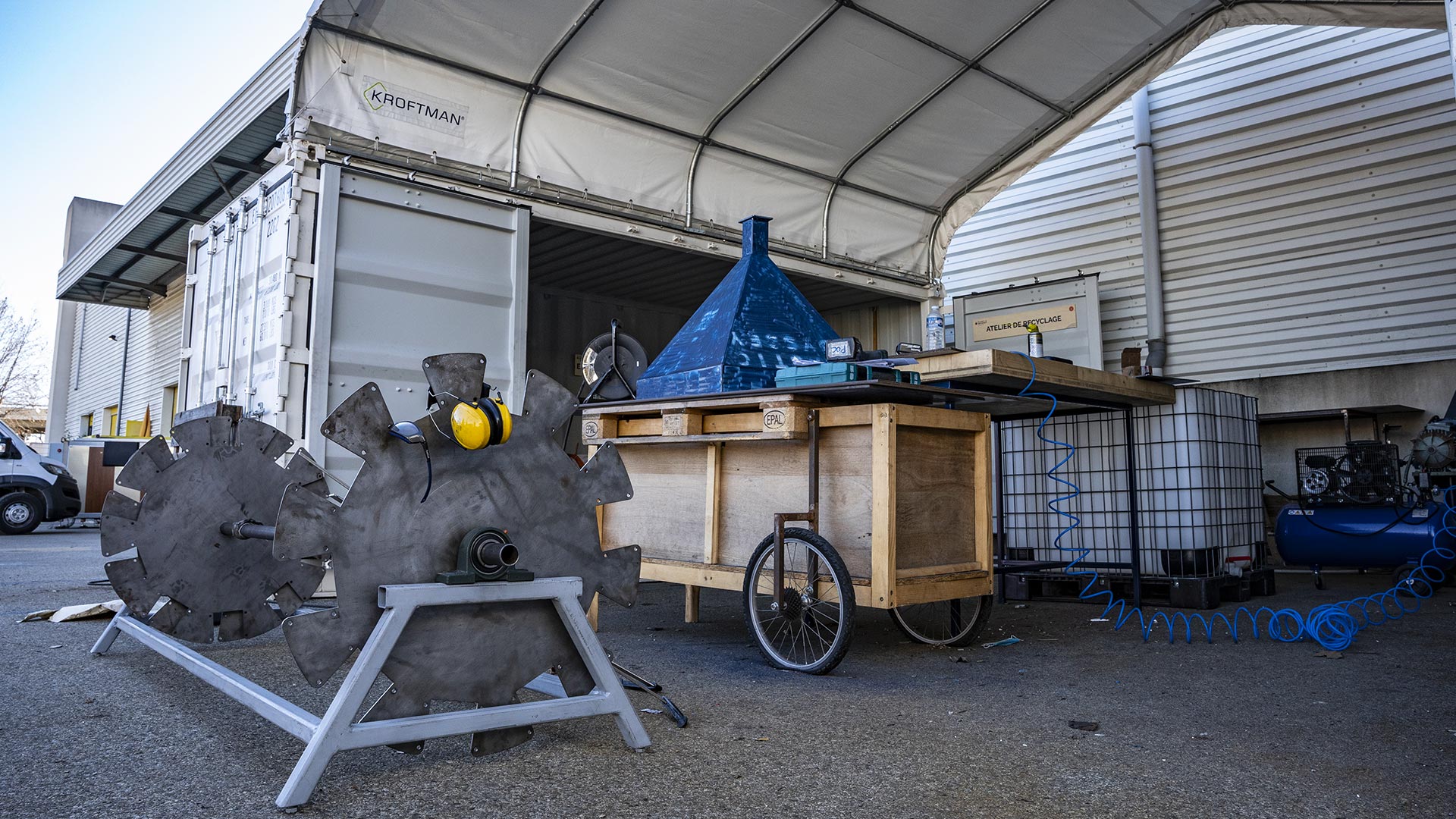
Mise à jour du mercredi 17 mars 2021
Des plans à l’installation à bord, découvrez l’histoire des machines
J’ai rejoint le projet il y a maintenant deux ans. Depuis, je travaille quotidiennement sur les machines de recyclage. Et avant d’obtenir des machines de valorisation qui correspondent à notre besoin, nous sommes passés par plusieurs étapes !
Sources d’inspiration, recherches et voyages d’étude
La première étape a été de définir quelles machines sont indispensables dans un processus de valorisation des déchets plastiques basiques. Il y a donc eu une première phase de recherche sur ce qui se fait dans l’industrie. Nous avons effectué plusieurs visites de centres de recyclage en France principalement, mais aussi en Allemagne et en Angleterre. Ça nous a donné une bonne idée des processus utilisés, mais aussi de la complexité de la valorisation, car chaque typologie de déchets nécessite une valorisation particulière.
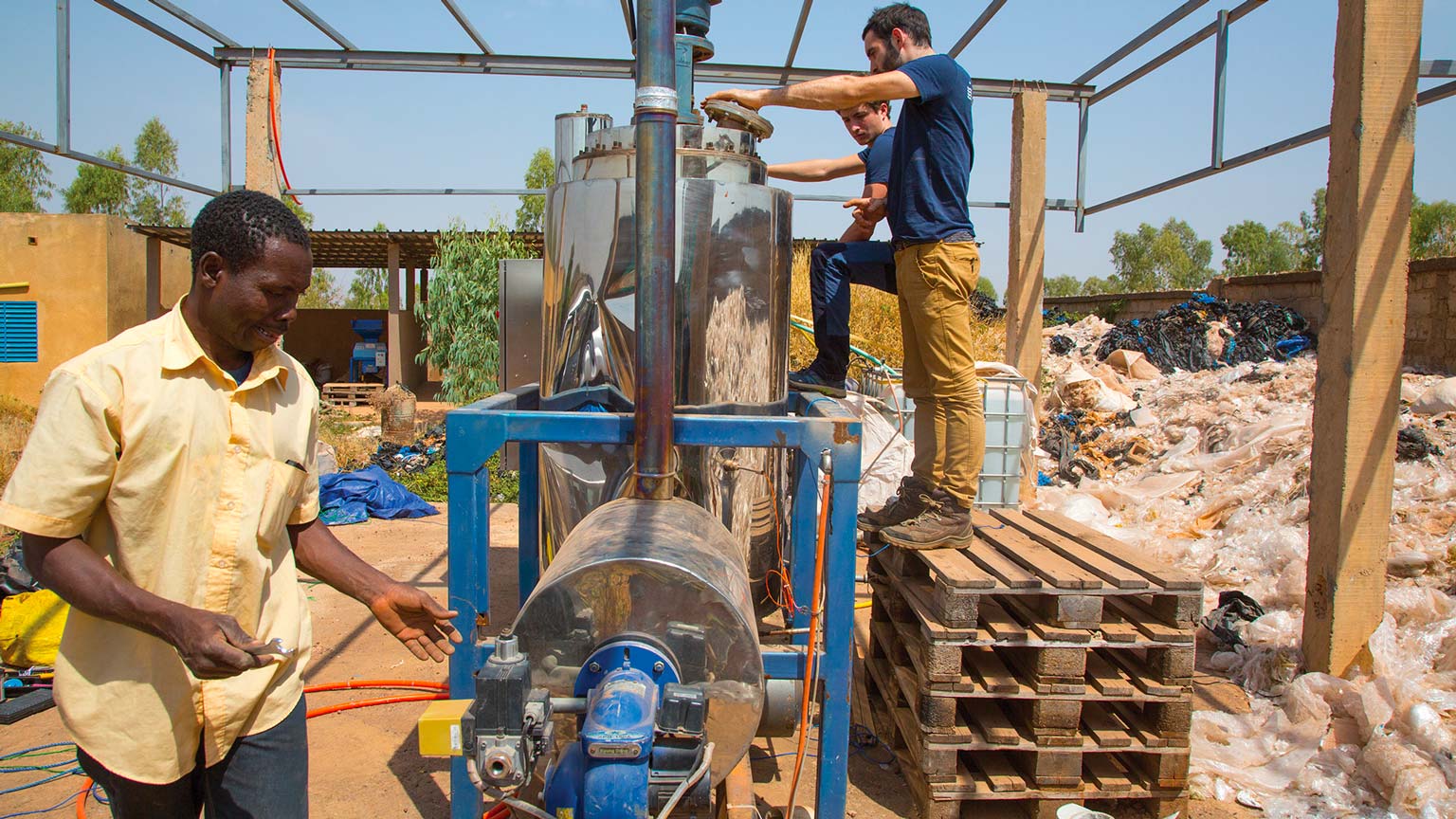
Nous nous sommes aussi et surtout rapprochés de ce qui existe déjà sur le terrain, à petite échelle et souvent dans des contextes informels. Nous avons contacté des dizaines de porteurs de projets de recyclage, en Afrique, Amérique du Sud et Asie. Nous avons eu la chance de pouvoir échanger longuement sur leurs actions, ce qu’ils utilisent comme processus, leurs retours d’expériences et la définition de leurs besoins. C’était une étape très enrichissante : nous avons énormément appris des différentes utilisations des machines sur le terrain, et nous avons compris que les machines elles-mêmes pouvaient être très différentes des machines industrielles que l’on avait pu voir en Europe.
Rencontre avec la communauté des Zabaleen en Égypte
L’étape suivante a été de réaliser des voyages d’étude au Burkina Faso, en Thaïlande et en Egypte. Ces voyages d’études ont été très importants car nous avons pu rencontrer les acteurs des écosystèmes locaux et en assistant à des démonstrations et des explications concrètes.
En Egypte par exemple, la communauté des Zabaleen travaille dans le recyclage de façon informelle depuis plus de 50 ans. Ils sont des milliers chaque jour à collecter, trier et valoriser les déchets du Caire. Ils ont une expérience tellement impressionnante qu’ils construisent eux-mêmes une partie de leurs machines de recyclage, notamment broyeurs et extrudeuses. Les broyeurs construits là-bas, on peut d’ailleurs les retrouver dans d’autres régions du monde où l’on travaille sur la valorisation. Notamment à Kinshasa, un projet de recyclage de sacs plastiques utilise un broyeur fabriqué au Caire !
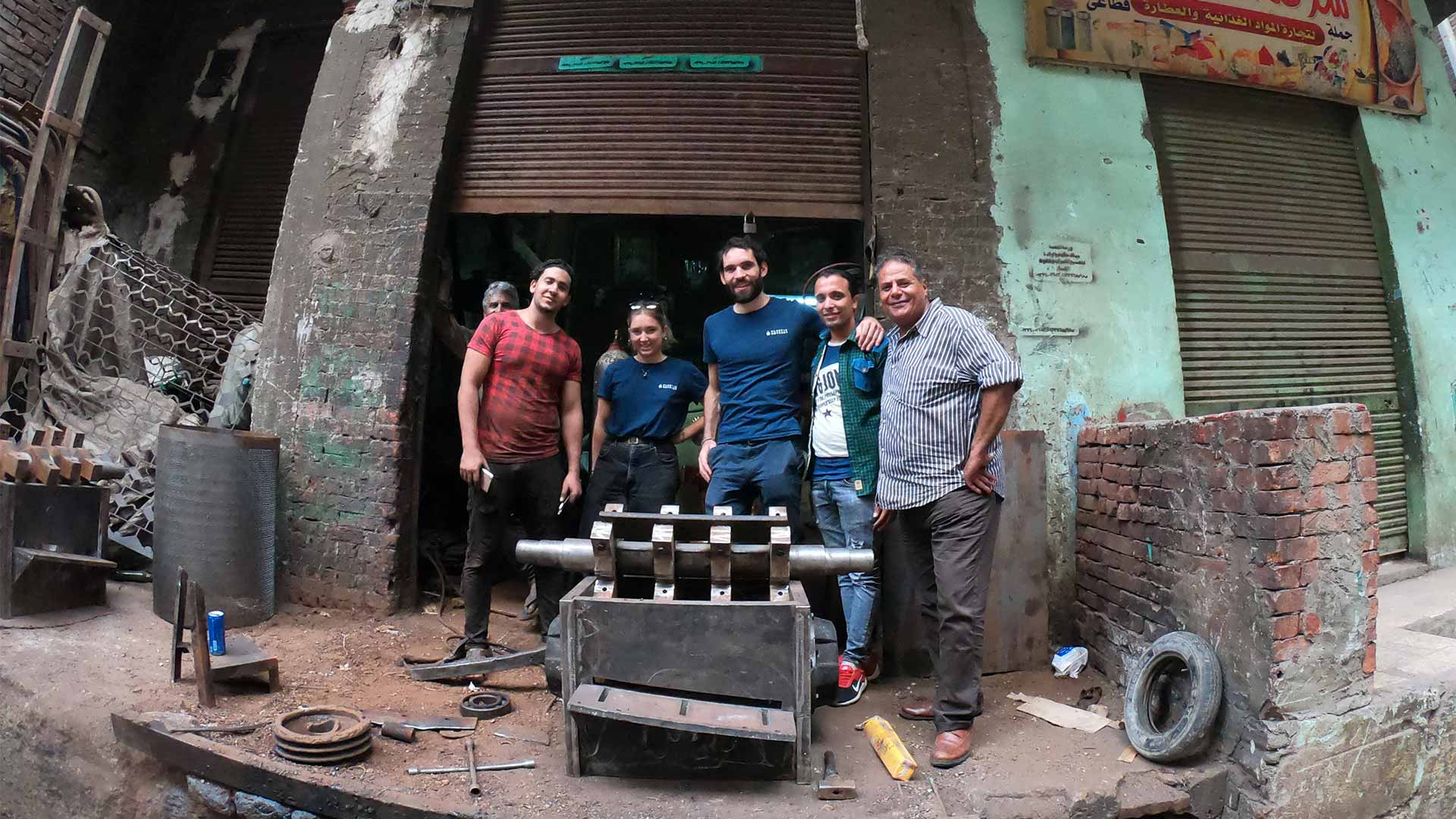
Grâce à cette démarche de recherche et d’études terrain, plusieurs exemples concrets d’application de nos futures machines de recyclage se dessinent. En plus, ces exemples nous permettent d’étudier le sujet pour des types de déchets assez variés.
Largement inspirés par tout cela, nous arrivons donc à identifier précisément les machines que nous embarquerons, pour répondre à nos critères de simplicité et de robustesse.
Conception, fabrication et documentation
Nous avons donc réalisé nous-même la conception à partir de ce que nous avions pu étudier, en y apportant quelques améliorations en termes de sécurité, et quelques adaptations nécessaires à l’embarquement à bord du navire Plastic Odyssey. La conception nous a permis de documenter l’ensemble des pièces, créer des mises en plan précises et se rendre compte des difficultés pouvant apparaître pendant la fabrication.

Notre obsession dans la phase de conception est de réduire au maximum le nombre de matériaux différents à utiliser pour la fabrication. Par exemple, le châssis de notre broyeur a été dessiné pour être fabriqué avec un seul type de barre en acier de section carrée. Aucune pièce du châssis ne doit-être découpée au laser : dès que l’on peut, on évite au maximum le sur-mesure.
La conception consiste à définir l’usage de la machine, puis à trouver des moyens technologiques pour répondre à cet usage. Il nous faut choisir les pièces, les dimensionner, définir les matériaux, vérifier que c’est suffisamment résistant pour l’usage que l’on en a, penser à la manière dont cela va être fabriqué et assemblé. On a la chance d’avoir des logiciels de modélisation pour dessiner les pièces et vérifier que le tout s’assemble correctement. Cela nous fait gagner du temps et de l’argent car l’alternative serait de faire plusieurs prototypes en physique, puis de les adapter.
L’exemple du Broyeur des déchets plastiques
Voici le dessin du broyeur en 3 dimensions. Celui-ci nous donne un aperçu assez précis de ce à quoi il va ressembler. Une fois que l’on a pensé à tout, on peut fabriquer chacune des pièces et les assembler.
Il y a bien sûr des surprises entre la 3D et la réalité, notamment le volume que ça prend dans l’espace, le poids de chacune des pièces, etc. Mais si la conception est bien faite et bien pensée en amont, les surprises sont rarement mauvaises !
Pour chacune des machines que nous avons fabriquées, nous sommes donc passés par ces étapes de conception, de modélisation et de mise en plan.
Mise à jour du jeudi 18 mars 2021
La fabrication des machines
L’aménagement de l’atelier à Marseille
Les machines ont été fabriquées en grande partie au sein de notre atelier marseillais : un espace de 50m² au sein de l’entrepôt de Lemon Tri – entreprise d’insertion qui s’occupe du tri et de la collecte des déchets dans les entreprises. Il a ensuite fallu équiper l’atelier, avec de l’outillage simple mais indispensable, de la matière première, tout ce dont nous avions besoin pour travailler sur la fabrication.
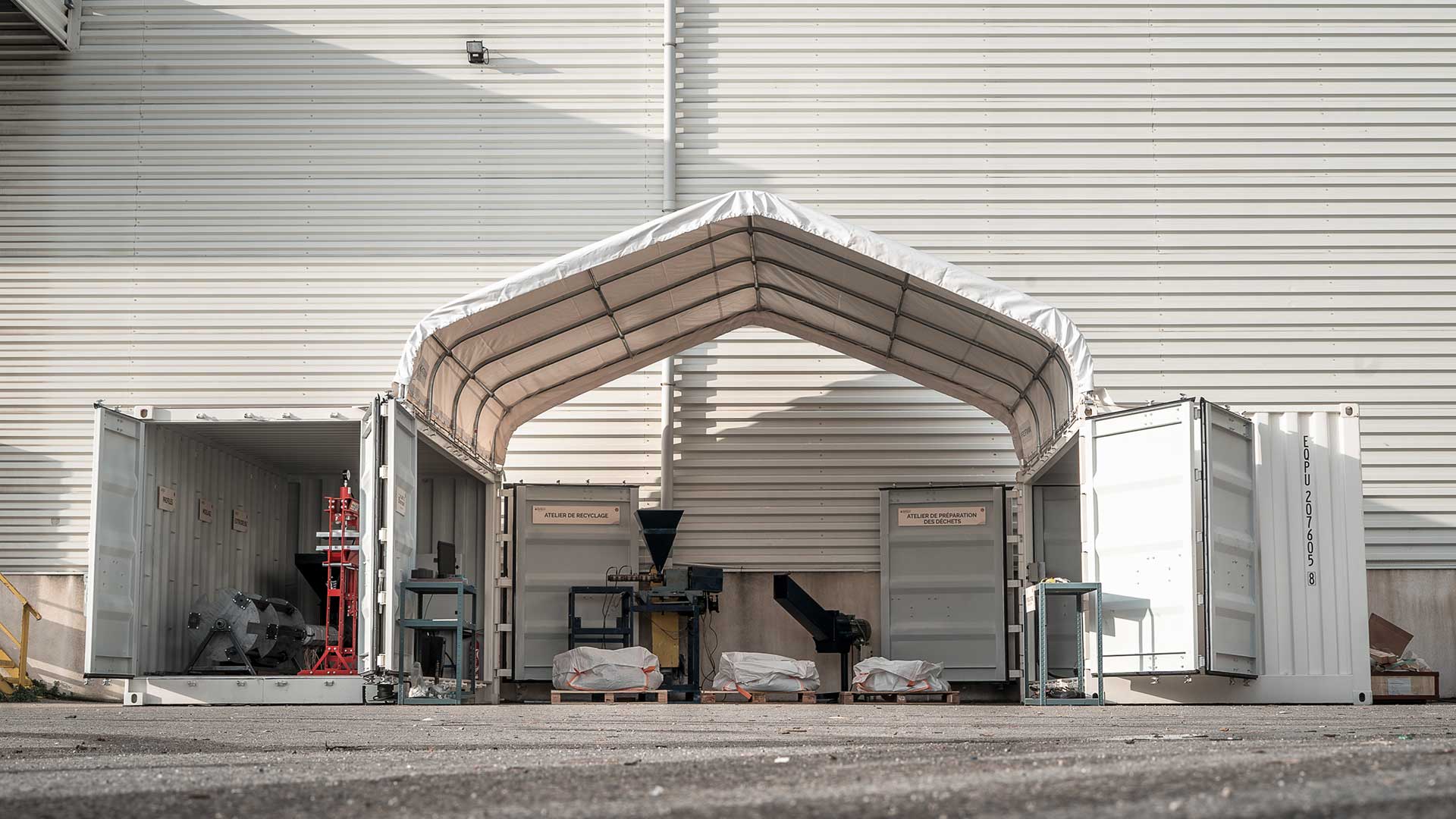
Les étapes de fabrication
À la suite des étapes de conception et une fois que les plans ont été vérifiés, nous nous nous attelons à la fabrication. Celle-ci se déroule en plusieurs étapes :
La première étape consiste à récupérer ou commander la matière première, les différentes pièces composant les machines, et les éléments spécifiques comme les moteurs ou les roulements. On essaye le plus possible de réutiliser ou récupérer des éléments. Pour le broyeur par exemple, il nous fallait tous les profilés en acier nécessaires à sa fabrication : les tôles, le moteur, les lames, la visserie, etc. Quand tout est réuni, on a qu’une hâte c’est de commencer à fabriquer !
Il faut ensuite préparer chaque pièce une à une. A partir d’un profilé carré en acier de 6 mètres, nous devons le couper en plusieurs pièces aux dimensions souhaitées.
Une fois que toutes les pièces sont prêtes, nous commençons l’assemblage par sous-ensemble. Le châssis, le support moteur, la trémie, le bac de récupération, l’axe, etc. Tout ça avec de l’outillage simple, un poste à souder et pas mal d’huile de coude !
Nous passons ensuite à l’assemblage complet en associant tous les sous-ensembles entre eux. La machine prend enfin forme. C’est à ce moment-là que l’on se rend compte du volume et de la place que cela va prendre à bord.
Il ne nous reste plus qu’à constituer l’armoire électrique et câbler électriquement le moteur. En France, nous sommes soumis à des normes de protection strictes. Les armoires électriques des machines sont simples, mais contiennent des composants nécessaires à la protection des personnes et des équipements.
Vient ensuite le temps des essais. Un peu d’appréhension mais beaucoup d’excitation au moment de brancher et de démarrer l’ensemble. Pas de casse, pas de blessés, ça fonctionne, tout va bien !
On procède finalement à quelques ajustements et on peut tout démonter pour emmener chaque pièce ou sous-assemblage en peinture. Dans le cadre de notre expédition, la peinture est indispensable car elle protège les machines contre la corrosion lorsqu’elles seront embarquées à bord du navire.
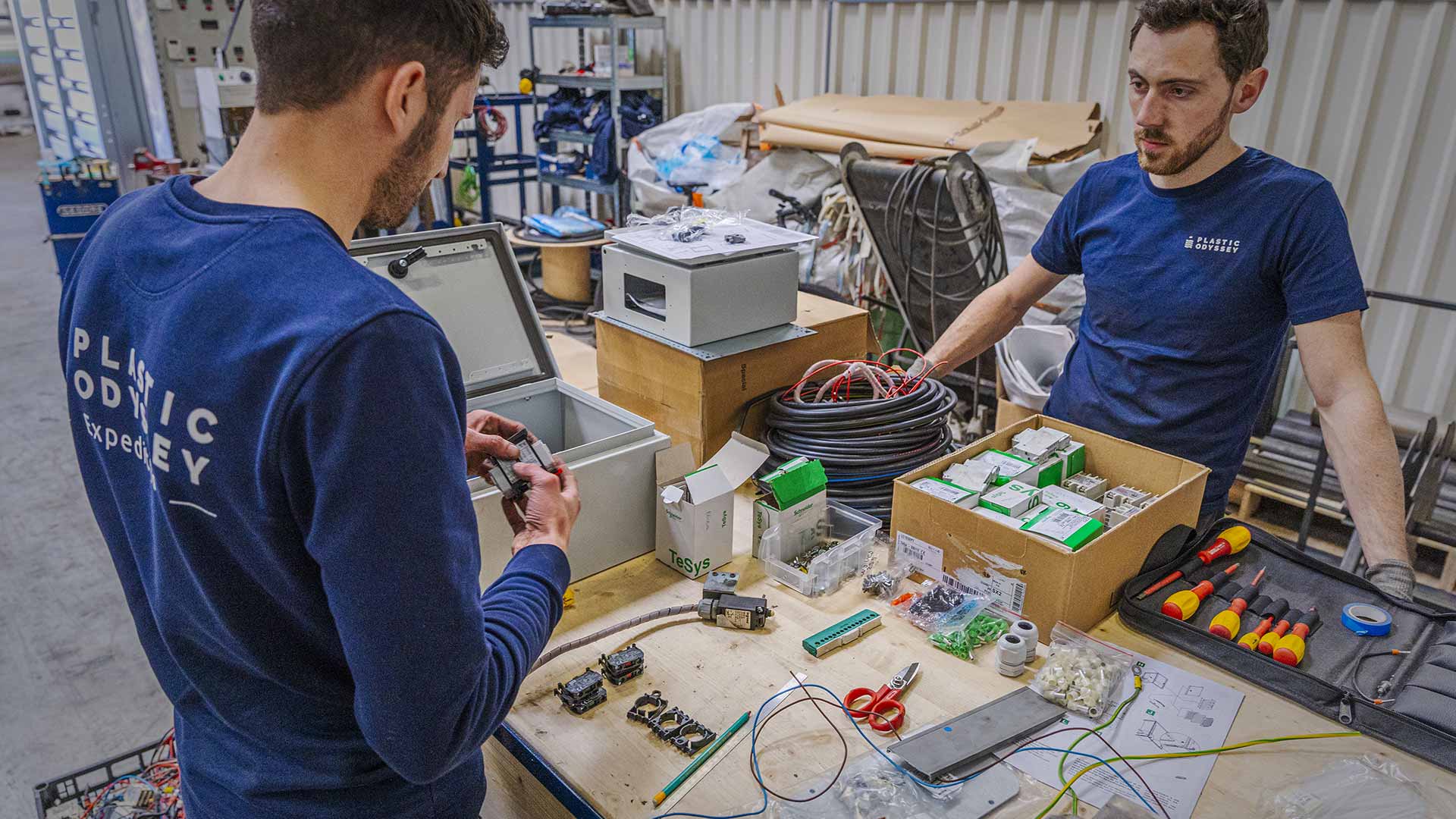
Coût et délais de fabrication
Dans notre atelier, nous avons fait naître la table de tri, le bac de lavage, le four à plaques, le barillet et nous avons réparé, modifié, adapté et testé l’extrudeuse.
Le broyeur et la centrifugeuse ont été fabriqués à la Cité des Arts de la Rue à Marseille, au sein des ateliers Sud-side. Leur expertise et les équipements dont ils disposent ont permis de fabriquer ces deux machines en seulement 2 semaines !
Dans l’ensemble, la fabrication de toutes les machines a été réalisée en seulement deux mois. Les processus de fabrication ont été rapides et peu coûteux par rapport à des capacités similaires dans l’industrie. Cela s’explique par des conceptions simples, l’utilisation d’un outillage basique et accessible, et par l’usage de matériaux standards que l’on retrouve partout.
À titre d’exemple, le broyeur de l’expédition, qui possède une puissance de 15 kW, nous a coûté près de 12 000€ à fabriquer en France. Environ 5 000€ de matériels et 7 000€ de main d’œuvre, ce qui représente 10 jours de travail à deux. Dans l’industrie en France, un broyeur de cette capacité se trouve aux alentours de 30 000€ minimum.
Mise à jour du vendredi 19 mars 2021
On y est presque !
Le navire a été remis à l’eau le 9 mars dernier, aux couleurs de Plastic Odyssey, l’heure est arrivée d’embarquer toutes nos machines qui constituent notre atelier.
Ceci marque une grande étape et beaucoup d’émotions pour notre équipe technique, la fin de 2 années de travail acharné.
Dans quelques semaines, suivez le montage des machines de recyclage sur le navire. Nous partagerons ces avancées en LIVE.
Pour terminer cet article en beauté, voici quelques images du montage et de la fabrication de notre broyeur.
Tom Bébien, Responsable de l’atelier de recyclage de Plastic Odyssey est en charge de la conception, de la fabrication et de l’amélioration continue des machines. Il travaille avec l’équipe technique composée de Bob Vrignaud, co-fondateur de Plastic Odyssey et directeur R&D, et Baptiste Lomenech, technicien plasturgiste. L’atelier de développement est situé à Marseille et les machines seront embarquées dans quelques semaines à bord u navire Plastic Odyssey.
Nos derniers articles
Comores : programme des événements à Mohéli, Moroni et Anjouan
Découvrez le programme de l'escale aux Comores, du 22 juin au 11 juillet, où de nombreux évènements sont organisés à Mohéli, Moroni et Anjouan ...
Plastic Odyssey et l’UNESCO unissent leurs forces pour dépolluer les sites marins inscrits au patrimoine mondial
Face à la montée de la pollution plastique, les 50 sites marins inscrits au patrimoine mondial de l’UNESCO sont eux aussi menacés. À l’occasio...
Apprentis Explorateurs : le programme pédagogique de Plastic Odyssey pour agir face à la pollution plastique
Un programme pédagogique en 7 activités, conçu par l’équipe de l’expédition pour sensibiliser les élèves de l’école élémentaire et du ...