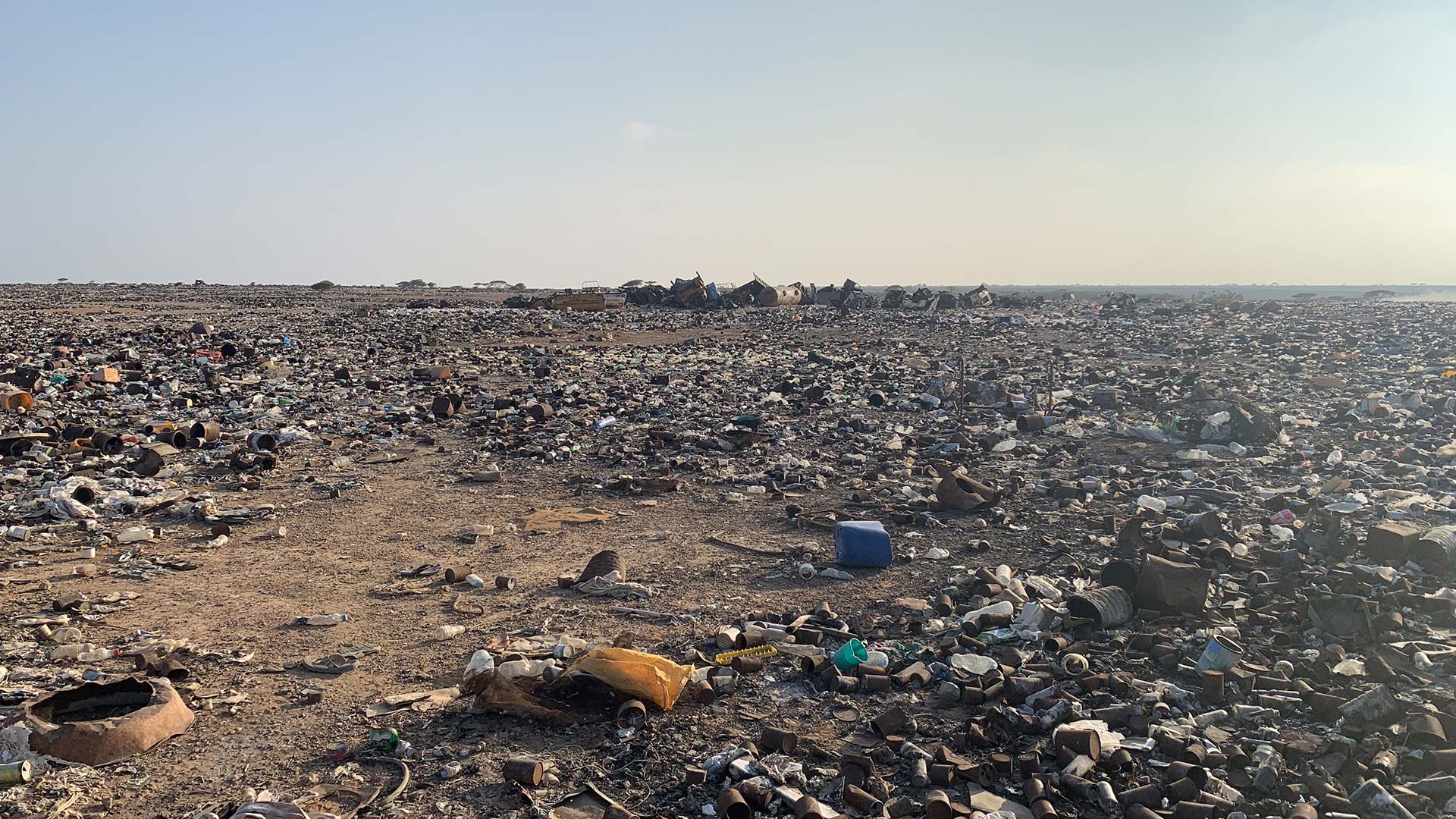
Local Factories: The third recycling micro-factory installed in Djibouti
An environmental preservation project for the most vulnerable populations
According to the French Development Agency (AFD), Djibouti is among the most urbanized countries in Africa, but social indicators are still very low, with three-quarters of the population living below the relative poverty line and over half in the capital.
In collaboration with local authorities, the IOM has established a plastic waste recycling unit to contribute to the cleaning of the city of Obock and environmental preservation. The aim of this unit is to transform the plastic generated by the city into construction materials (pavers and concrete blocks) beneficial for the urban development of the city and the country. Currently, a total of five employees are involved in the process of transforming plastic waste into pavers. The sale of these end products is expected to ensure the profitability and long-term operation of this unit. To start production, the IOM has invested in a micro-factory to transform plastic into pavers.
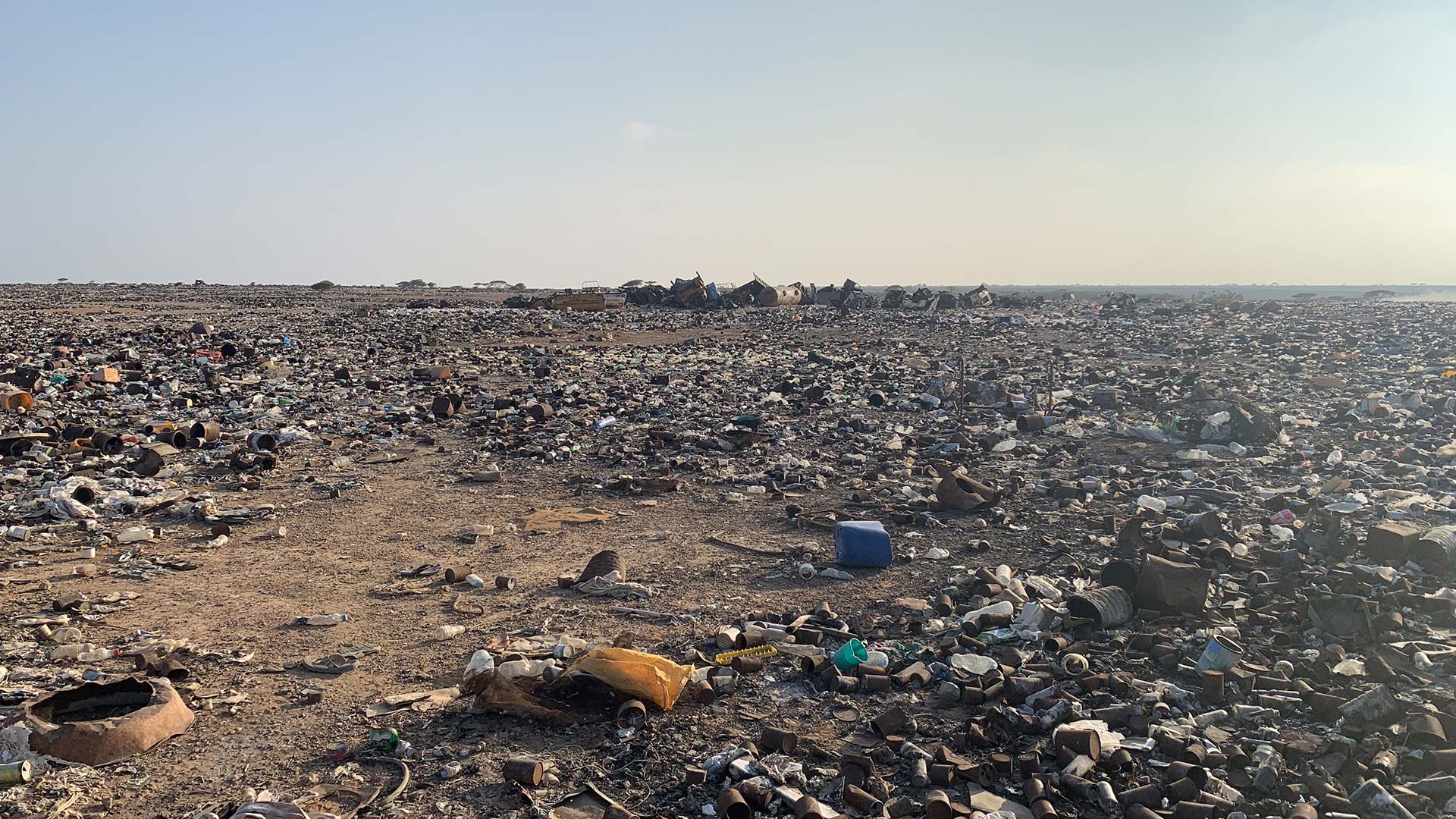
In addition, to ensure plastic collection in the city, the IOM has implemented a “Cash for Work” system by employing 30 collectors from the most vulnerable community in Obock, selected based on eligibility criteria, who are paid according to the amount of plastic collected.
This activity is carried out as part of the project “Sustainable Solutions for the Most Vulnerable Host Populations, Refugees, and Migrants in Djibouti,” funded by the European Union Trust Fund.
Among the strong partners of the project is the company Coubèche based in Djibouti City. Coubèche is one of the largest companies in Djibouti and one of the few subsidiary companies of The Coca-Cola Company in Africa. Its role in Djibouti includes PET bottle blowing, bottling products for The Coca-Cola Company, and distribution throughout the country. They are the sole distributors of Coca-Cola, Fanta, and Crystal bottled water and supply Obock every week. Coubèche helped purchase a baler to compact PET bottles. These plastic bales will be bought back by the company to be recycled in their company located in Djibouti.
The regional council and the prefecture are also aware of the project and provide their support.
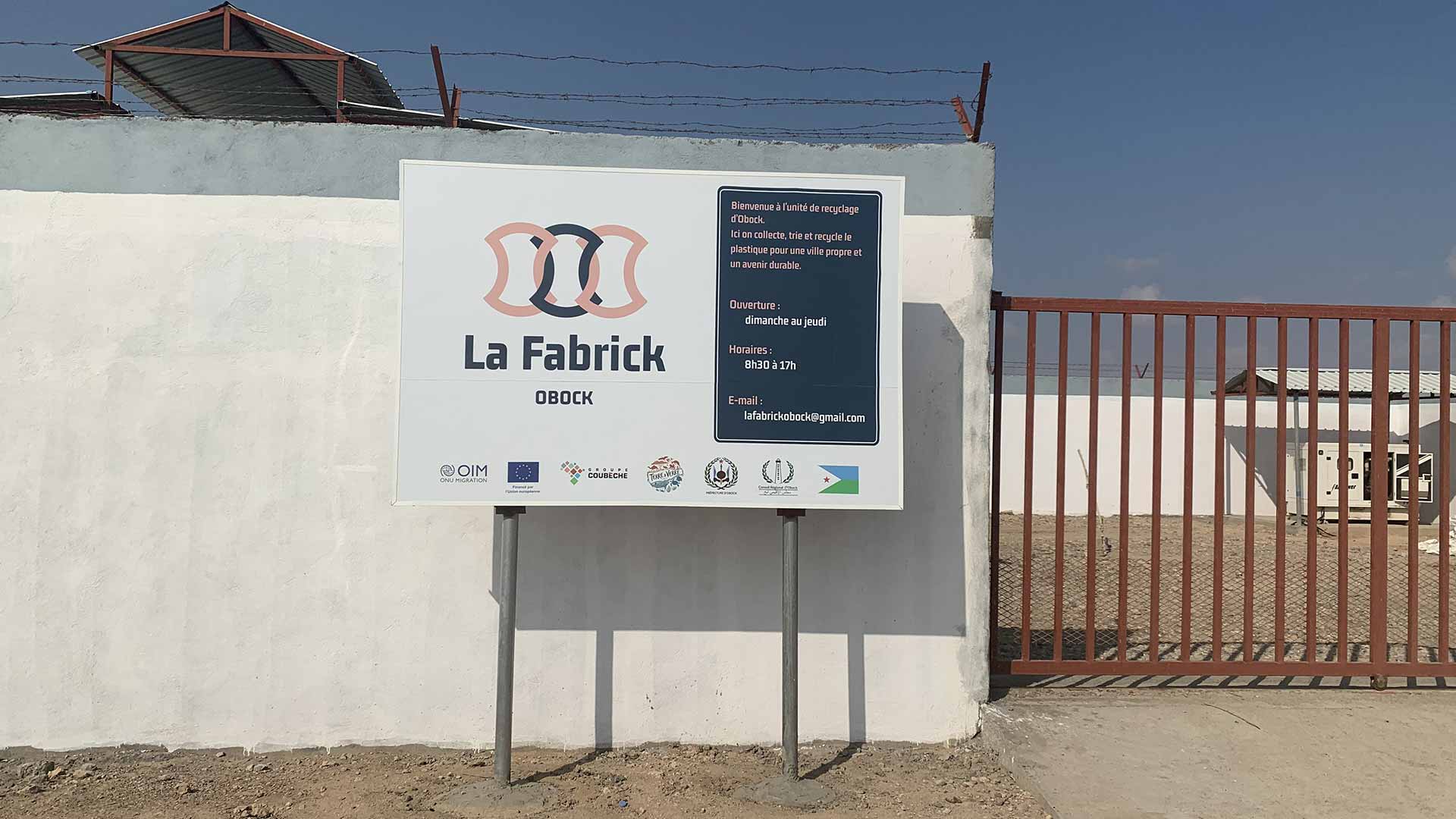
In the long term, The Fabrick recycling center can be supervised by the regional council, which will ensure the management of the center as well as the monitoring of the employees. The technical high school in Obock is also interested in participating in the project, particularly through technical internships offered to high school students. They will thus be trained in recycling and equipment maintenance. Finally, there is interest from the prefecture as well as the ADDS (Djiboutian Agency for Social Development), which could be customers if the manufactured products are competitive and meet their specifications.
The Fabrick, a recycling unit transforming plastic waste into interlocking pavers
The Fabrick currently transforms plastic waste into interlocking pavers. This object was chosen because construction materials are an identified need within the city, which regularly hosts construction projects such as sidewalks, roads, and housing. There is already a main paved road and a few paved sidewalks in Obock.
However, the current solution used is very artisanal and not highly optimized as it involves using a charcoal-heated pot and mainly unsuitable plastic waste such as plastic bottles. Both the capacity and quality of production are greatly affected by this process, and the need to switch to a better-calibrated solution is strongly desired. It is within this context that the Plastic Odyssey team has joined the project.
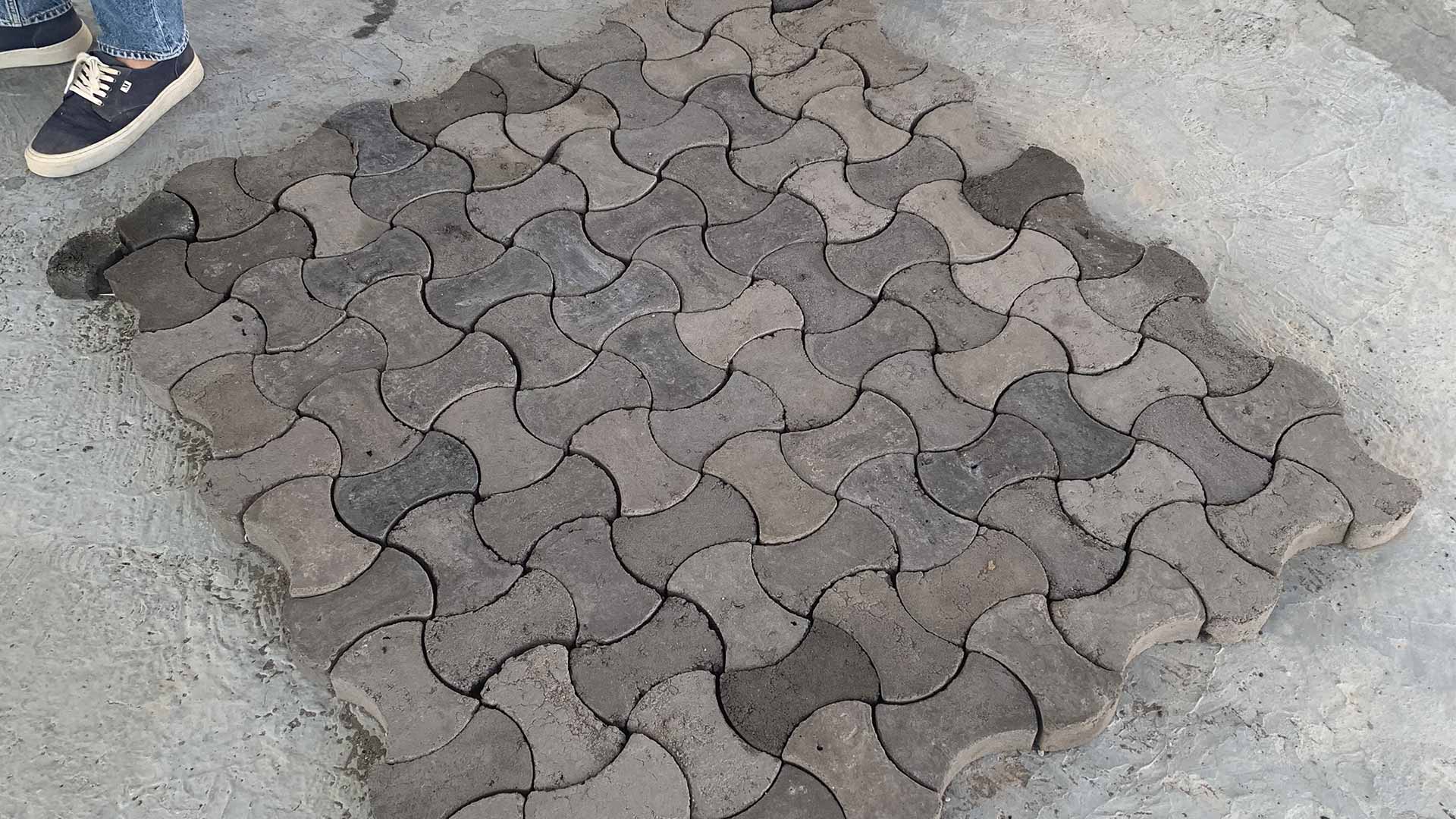
Field study and recommendations
During a week in Obock, Tom Bébien, Technical Manager at Plastic Odyssey, was able to conduct a technical and economic study to better understand the needs and make a recommendation for the most suitable device.
A more precise characterization of the plastic waste source was conducted in the Obock area, along with a study of potential markets and partners.
Among the potential markets, pavers appear to have a proven local market due to their simplicity and universal use. Furthermore, the employees at The Fabrick already have expertise in producing pavers, which simplifies the continuity of the activity.
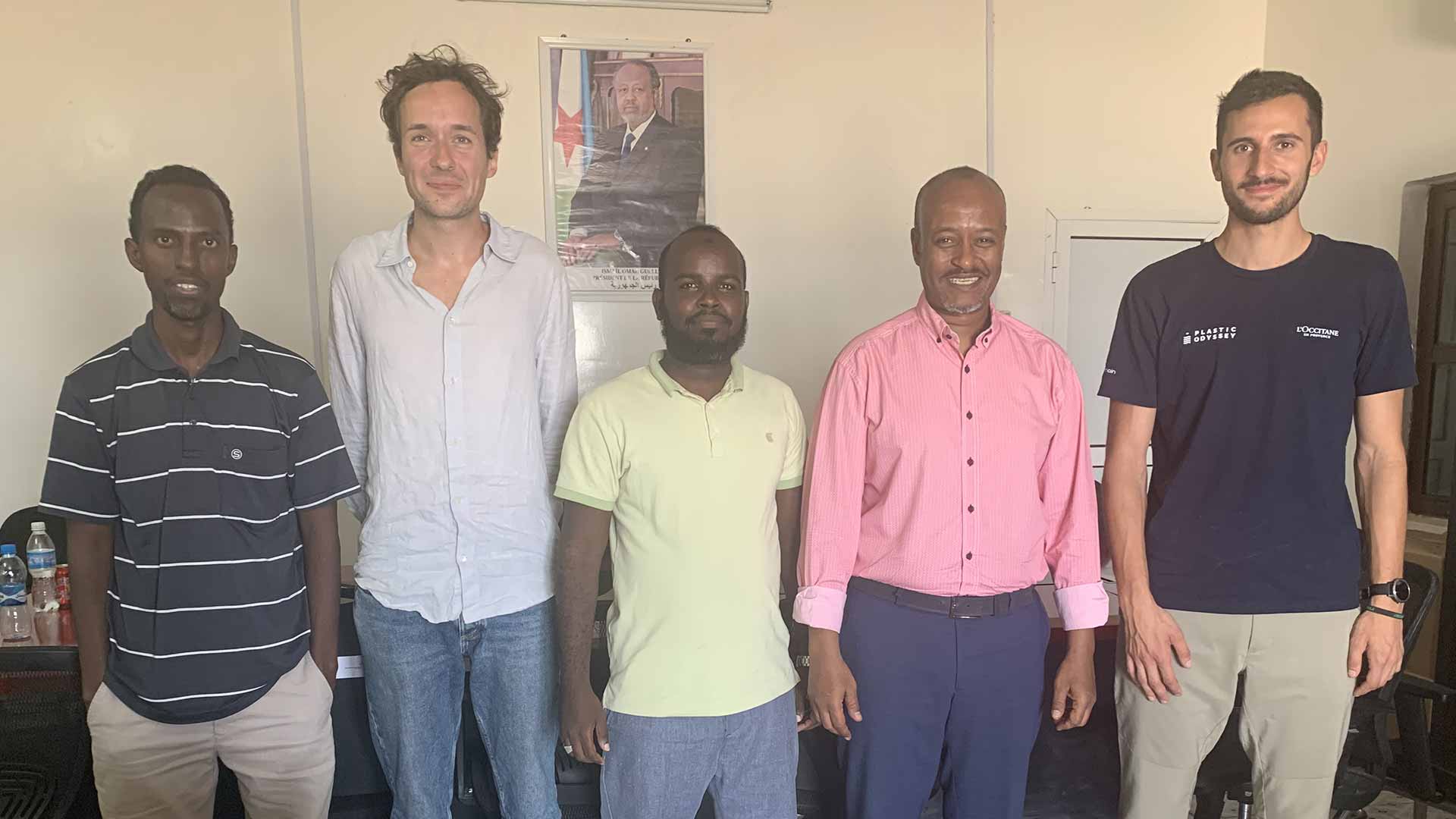
Following discussions with the prefect and the president of the regional council, the importance of accessing high-quality markets and having a profitable production economic model was emphasized. During these discussions, exploring possibilities to manufacture tiles or roofing sheets for houses, bricks for construction, and jerrycans for edible oil was also requested.
Other potential markets can be considered in the future
As a result, a more specific sorting between PE/PP, PET, and other plastics will be carried out. Waste in HDPE, PP, LDPE will be used for the production of pavers and joining pieces, while PET bottles will be resold as compacted bales to the Coubèche group.
Manufacturing and shipment of the container
The containerized micro-factory was manufactured in our workshop in Marseille. The recycling unit contains all the necessary equipment for transforming plastic waste into pavers. It will process approximately 50 tons of PE/PP plastics per year, with a production of around 500 pavers per day.
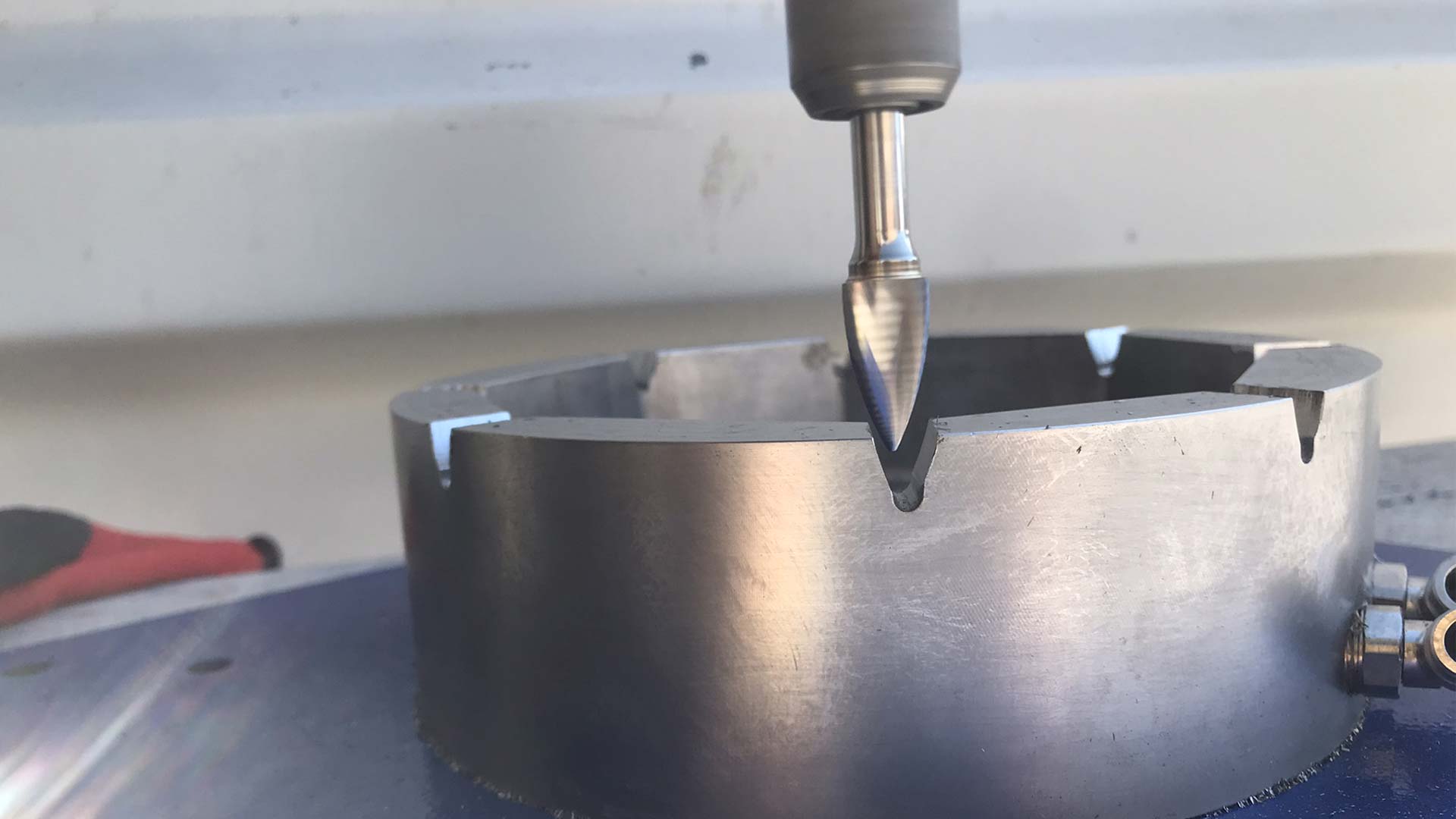
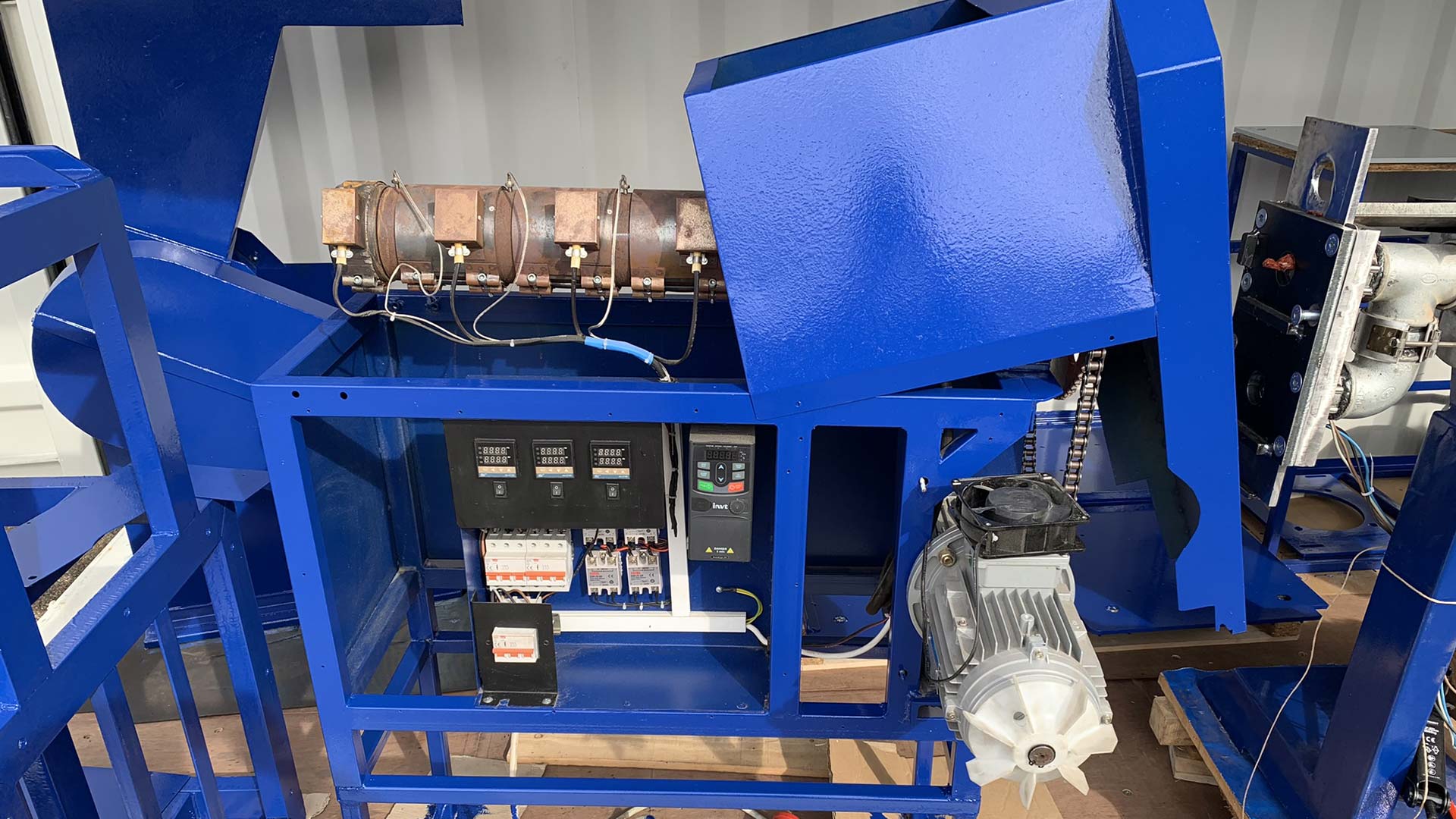
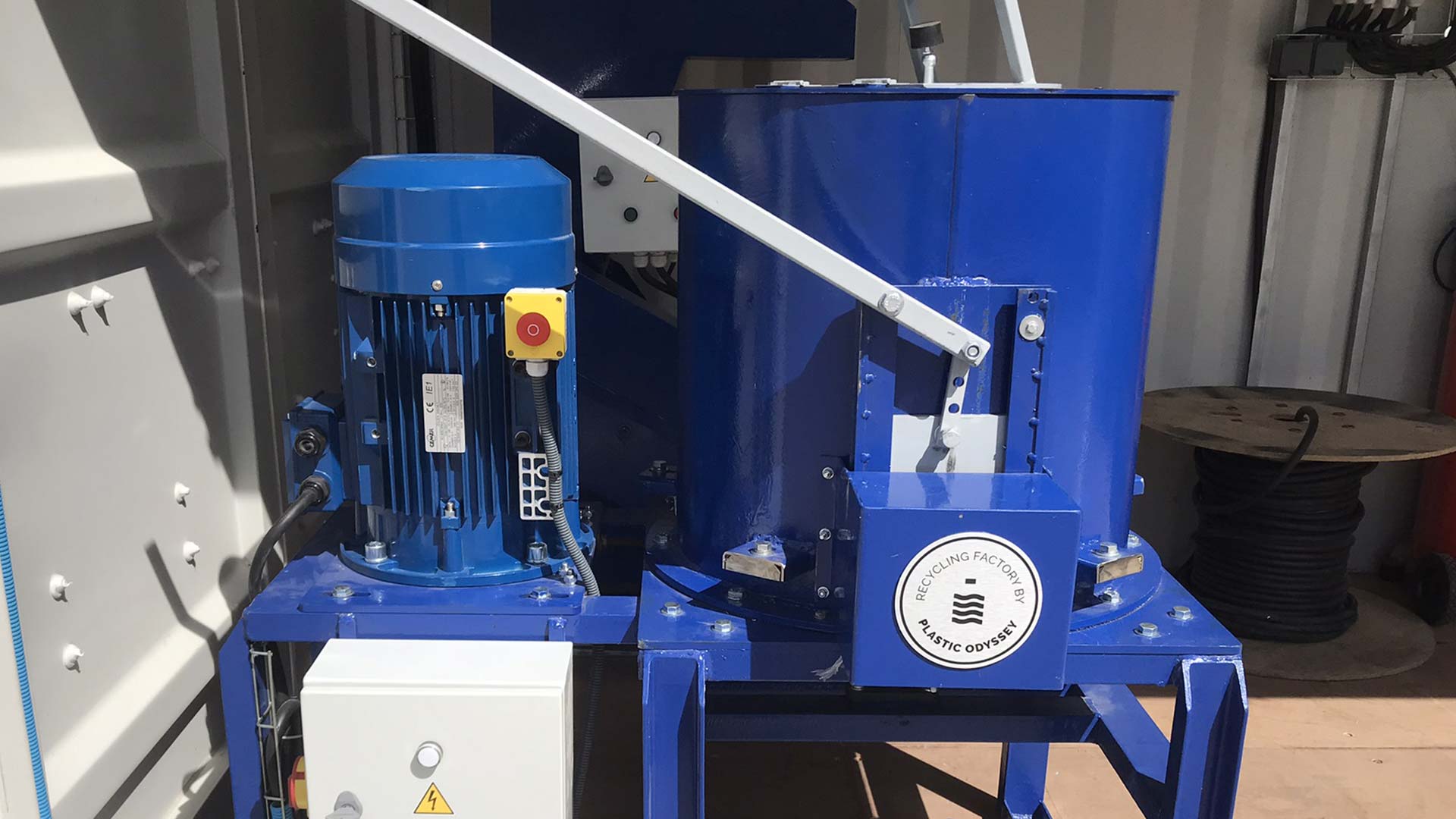
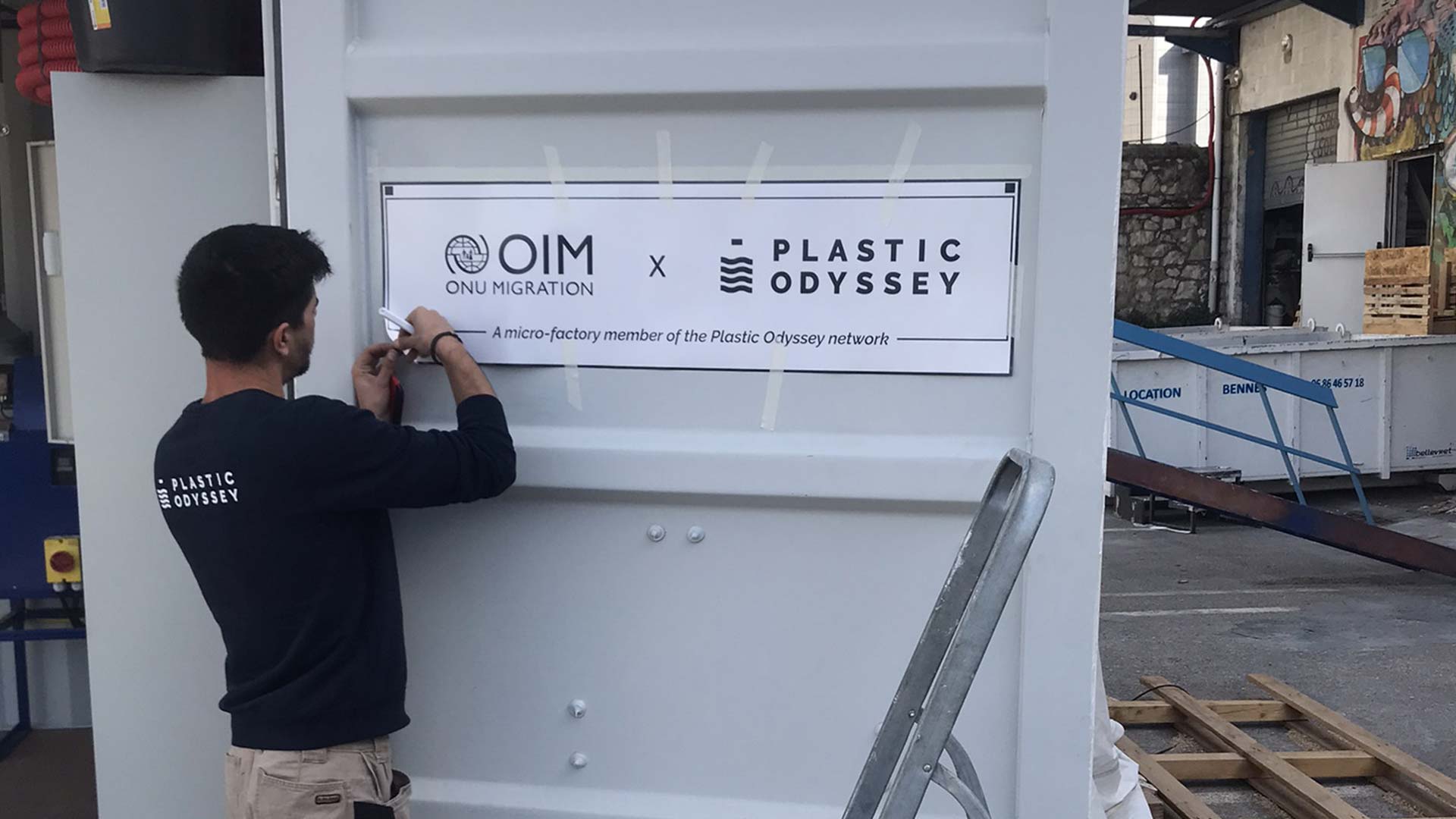
Low-tech Machine Presentation
This containerized micro-factory consists of all the machines and tools required to transform plastic waste into pavers. including:
- A shredder to reduce plastic waste into chips. A plastic-sand mixer to homogenize the mixture of plastic. In this form, they can be more easily stored and recycled.
- An agglomerator to reduce flexible plastics into small pieces. Plastic films and bags can come in various sizes and shapes, so they are agglomerated into uniformly sized pieces. In this form, they can be more easily stored and recycled.
- A plastic-sand mixer to homogenize the plastic and sand mixture, which is previously weighed to obtain the desired exact proportions. The mixture is then poured into the extruder’s hopper.
- An extruder to melt the plastic material: extrusion involves gradually heating and mixing the plastic chips and sand until they form a malleable paste that will then be shaped and cooled to create the pavers.
- Two pneumatic presses to shape the plastic material into molds: the hydraulic press molds the melted plastic coming out of the extruder or the hot plate and thus manufactures a new object from recycled plastic. The presses can press pavers of various sizes and shapes, only the molds need to be changed.
Other equipment present in the container is used for the proper functioning of the process, the safety of the operators, and the proper use of the machines. This includes a suction and ventilation system that extracts potential fumes from heating the plastic, a compressor and a storage cabinet for tools and equipment, personal protective equipment (PPE), and all the necessary materials for equipment maintenance.
Commissioning of the recycling micro-factory
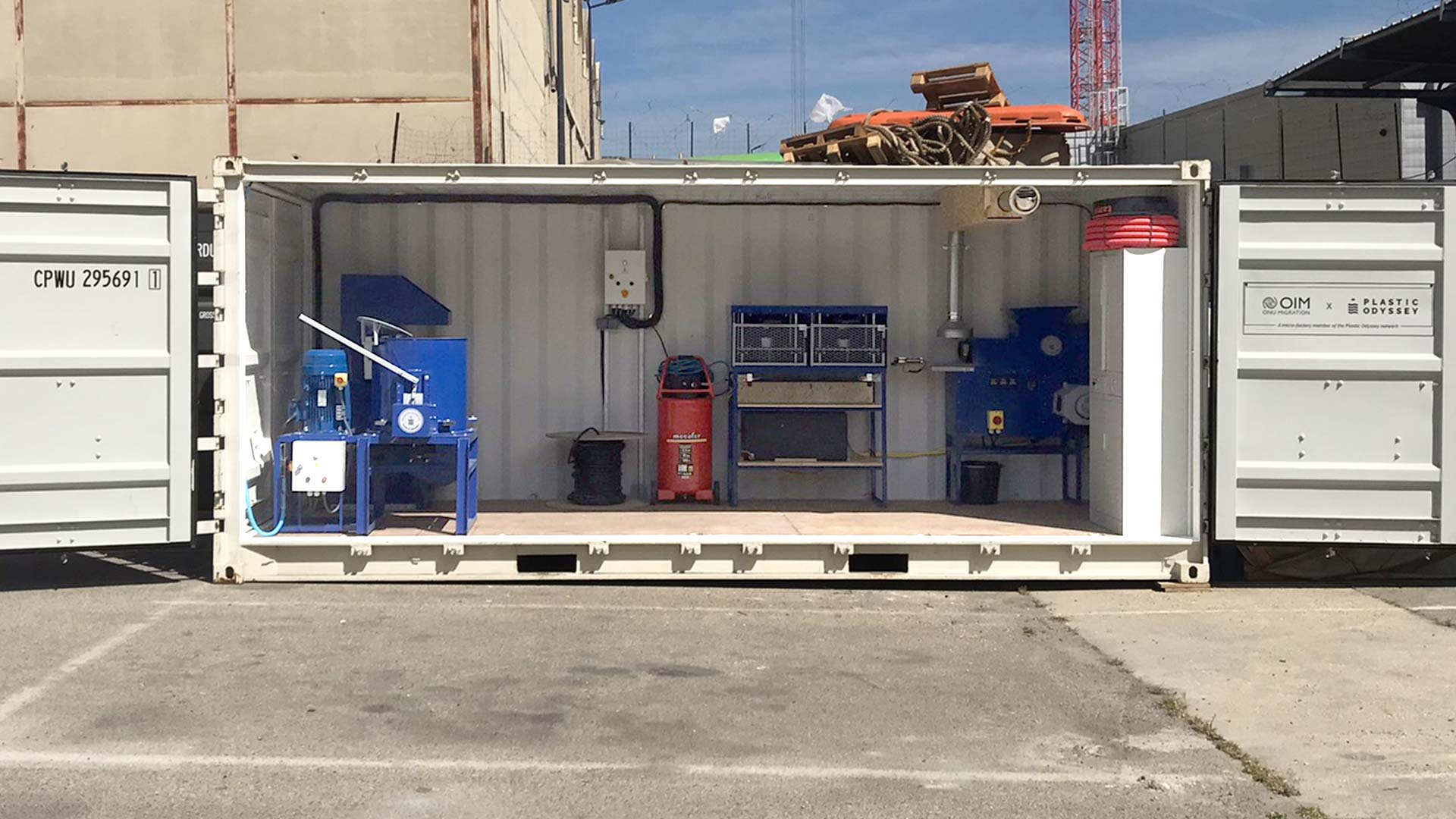
The recycling microfactory was shipped from Marseille on April 27, 2023 and arrived in Djibouti on June 5. Tom went on site to supervise the installation and train the teams.
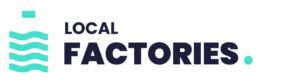
The Plastic Odyssey Local Factories are inspired by innovations and systems used on the ground around the world. They bring together, in the form of a container, all the machines necessary for the transformation of waste into new material or object.