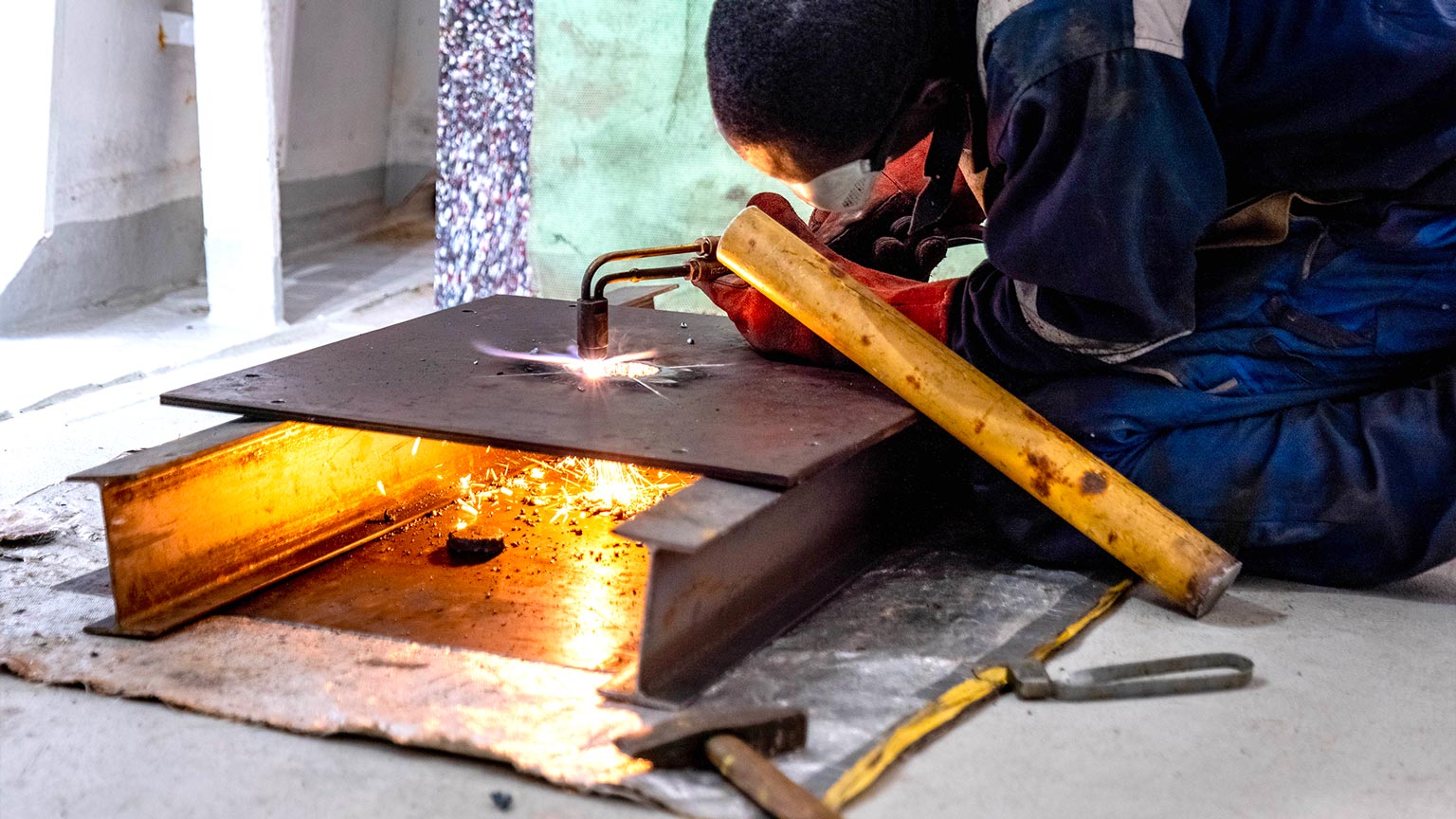
Stopover in Dakar: One month to locally manufacture two new recycling machines
Recycling technologies using second-hand materials.
To this day, all the low-tech machines on board the ship have been built in France. Thus, the challenge was to locally build these new machines using second-hand materials. We chose this approach because Dakar is filled with flea markets, workshops, and scrapyards where Senegalese people can find mechanical parts at unbeatable prices. For Plastic Odyssey’s technical team, it was a unique expedition into the depths of Dakar’s peri-urban mechanics. Building these machines in the informal ecosystem of second-hand materials was both a challenge and an opportunity to prove the low-tech characteristics of these recycling machines. After a few days of scouting in the hidden alleys of industrial areas, essential contacts, and material supplies, the manufacturing of the machines could begin.
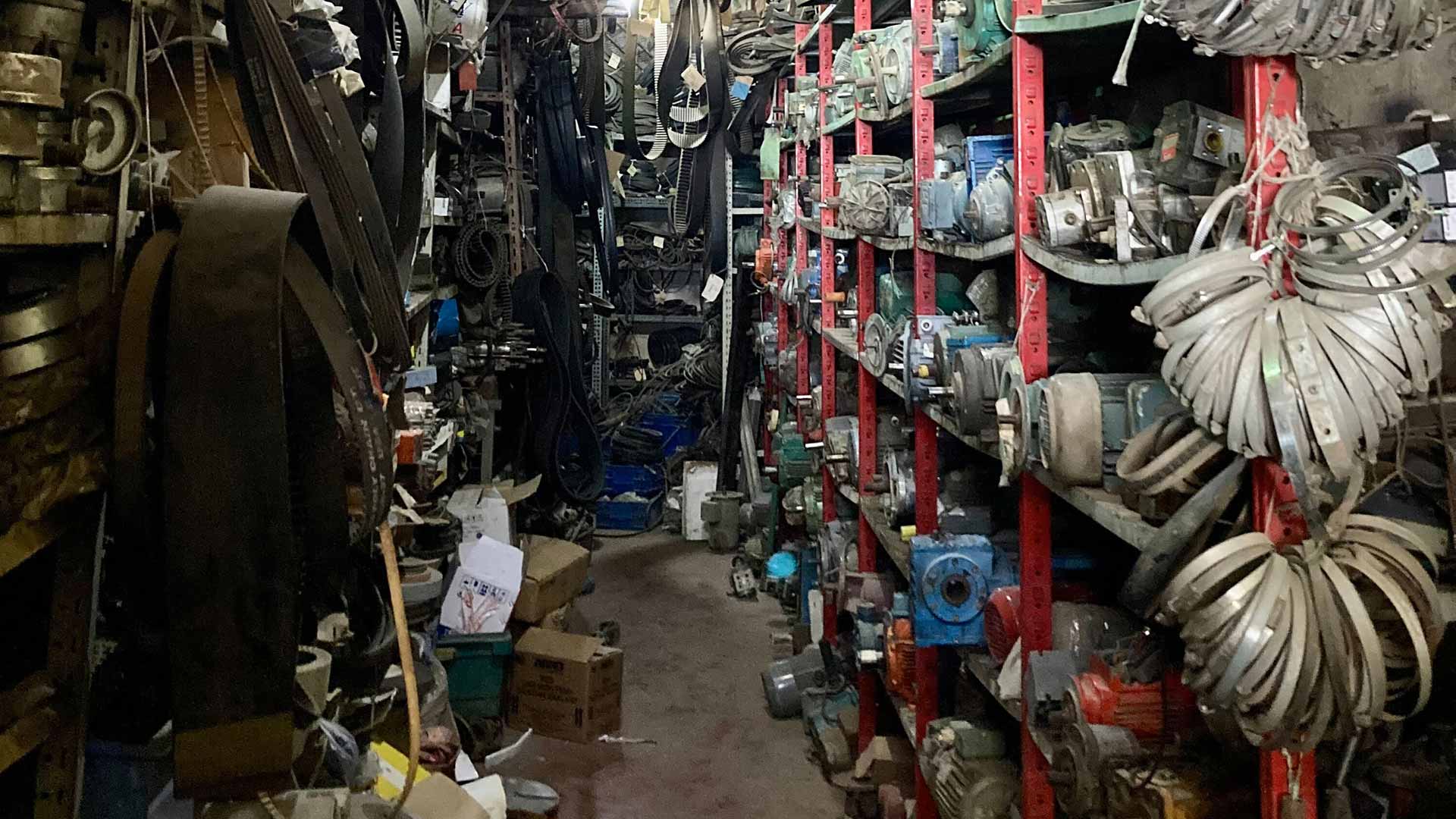
Manufacturing of a plastic agglomerator and a plastic-sand extruder.
The first machine was built on board the ship itself to experiment with the manufacturing capabilities and limitations of the laboratory vessel.
The second machine was made in collaboration with a small family workshop in Pikine, near Dakar. It was essential for the technical team to be able to work together with Senegalese technicians. Each stopover is an opportunity to exchange ideas about work methods, to share and learn about know-how and soft skills. It is within these small informal workshops that the heart of the Plastic Odyssey project lies: exploring, discovering, and understanding new low-tech “gems.”
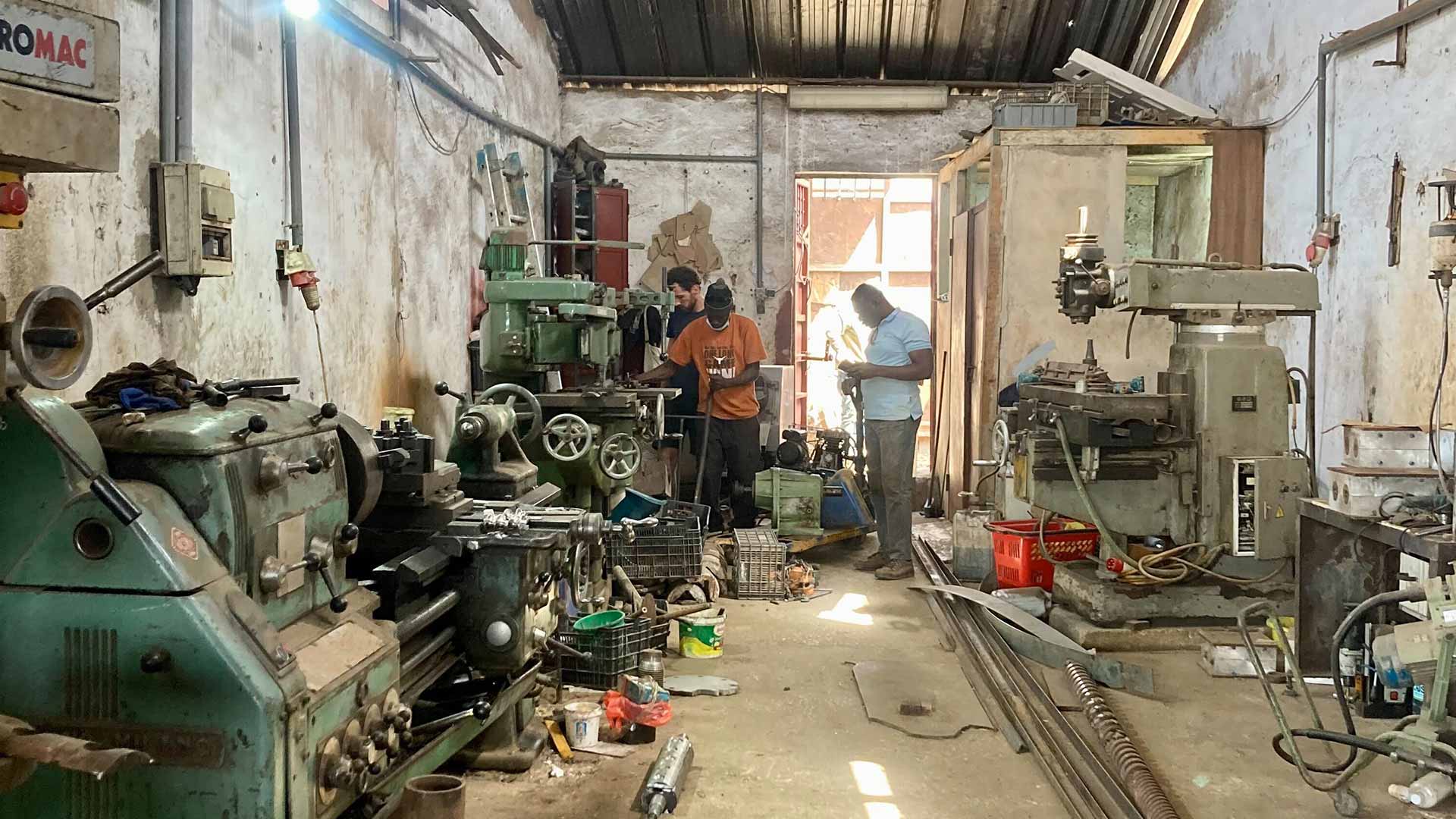
It was notably during the previous stopover in Morocco, in a workshop in Tangier, that a machine called the “agglomerator” was jointly studied with the technical team. The manufacturing of this machine was identified as essential for the ship’s onboard recycling chain. On board the ship, the manufacturing of the agglomerator was carried out by Roosevelt, a trainee mechanic from Benin, and Maxime, a new R&D engineer on the technical team. The agglomerator is a machine used to densify soft plastics from the LDPE (Low-Density Polyethylene) family, such as bags and packaging films. The plastics, previously collected and sorted, are introduced into a tank where the material is cut and heated using a system of rotating and fixed blades.
After this operation, the plastics are recovered in the form of pellets ready to be transformed into a new recycled object.
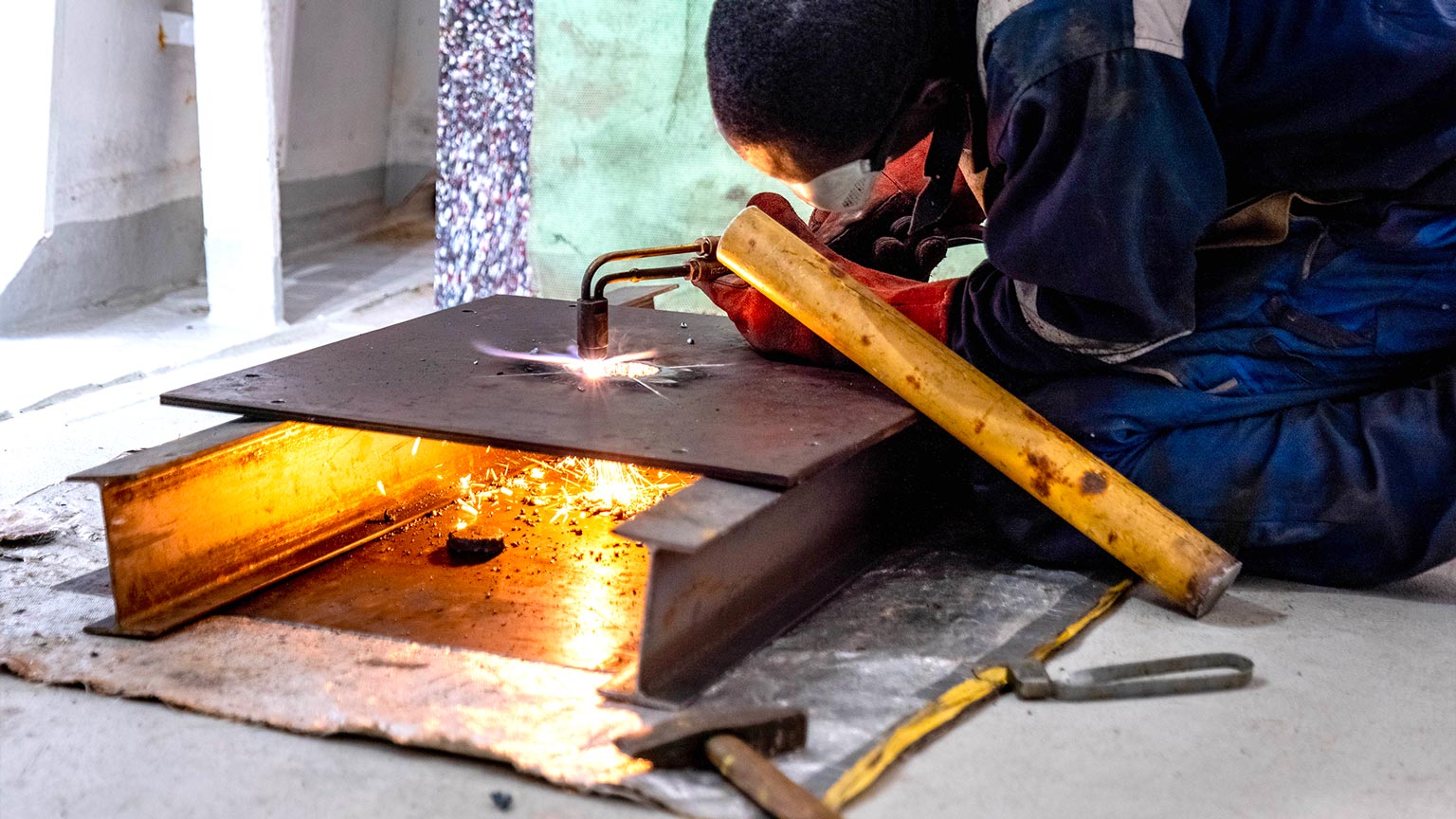
In the workshop in Pikine, Baptiste, the technical manager of the expedition, launched the Franco-Senegalese construction of a plastic-sand extruder. The extruder heats the previously crushed, washed, and dried plastic and mixes it with sand. This operation is carried out at a temperature of over 220 degrees Celsius. At the output of the extruder, a malleable paste is obtained, ready to be shaped into construction materials such as paving stones and tiles. These paving stones and tiles are formed using aluminum molds, which were machined in the Pikine workshop.
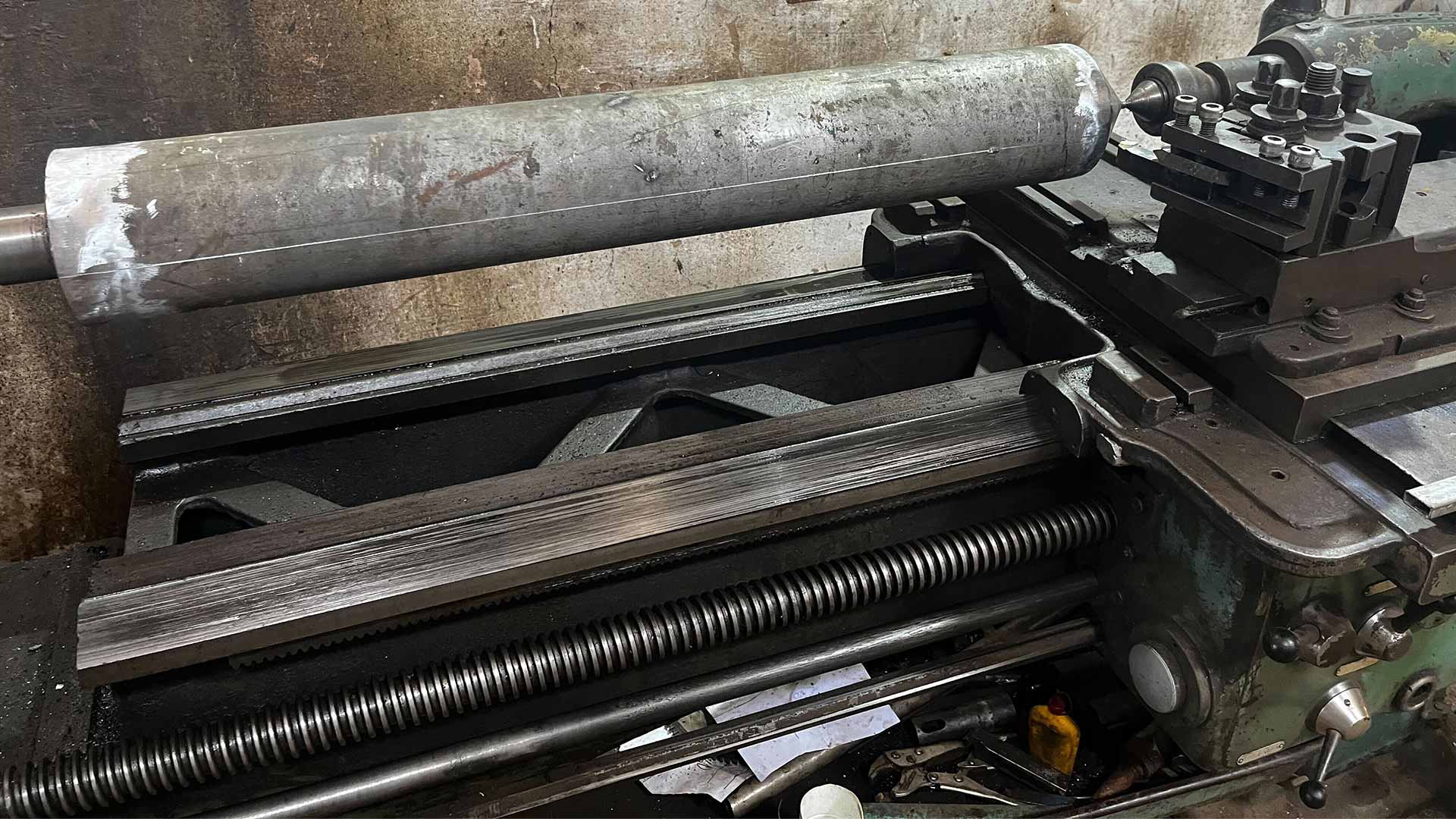
Two new recycling machines on board the ship.
The stopover in Dakar ended on March 27, 2023 for the Plastic Odyssey ship, and aboard its onboard workshop, two new recycling machines were created. Goal achieved!
The stopover was one of the most intense for the technical team, who had to agilely juggle between training entrepreneurs, technical partner visits, on-site company visits, and the manufacturing of the agglomerator and extruder.
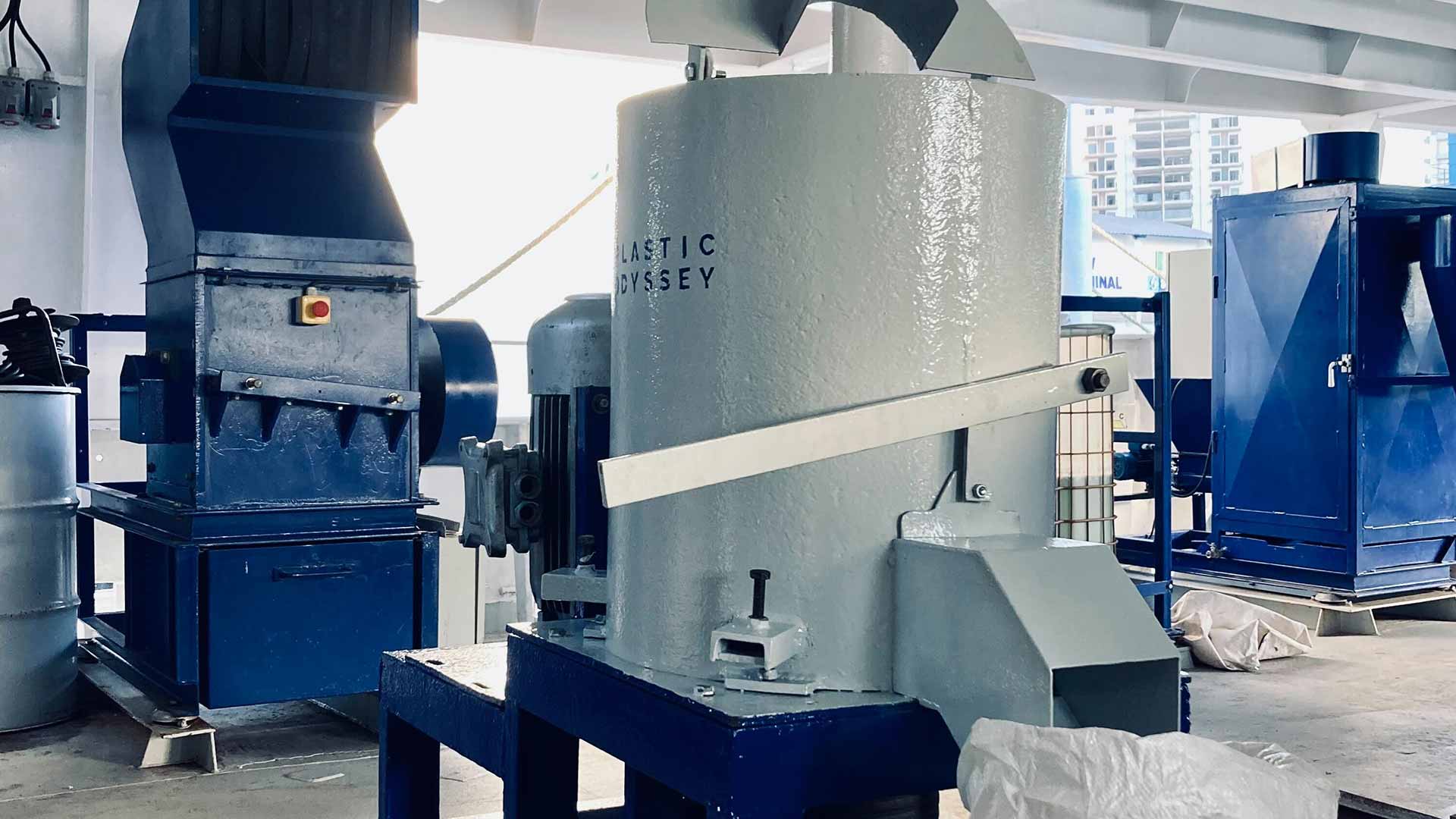
These two new machines complete the recycling chain on board the ship. From now on, experiments on the recycling of PEBD can be carried out continuously and will be open to training for entrepreneurs.
The plastic-sand extrusion will allow the development of the ideal recipe for the production of resistant and durable tiles and paving stones.
About the autor
“Coming out of a general engineering training, I have constantly learned and evolved in a structured and formalized system. In Dakar, a completely different world opened up to me, a kind of mechanical jungle! Day after day, meeting after meeting, I adapted to the informal second-hand market, a market with almost endless opportunities for low-tech. In a few weeks, we managed to build these two machines with very few technological and budgetary resources, all that remains is to document the manufacturing processes and make them accessible to everyone.”
Maxime – R&D engineer
Latest News
Tanzania: building a local recycling industry
Discover the plastic waste recycling entrepreneurs who participated in the training program aboard the ship in Das es Salaam, Tanzania....
The Global Plastics Treaty in Geneva: No Sleep, No Treaty
The UN Plastics Treaty is intended to become the first legally binding global agreement to end plastic pollution. Negotiations have taken place throug...
Comoros: An Archipelago In Search Of Sustainable Waste Solutions
Discover the plastic waste recycling entrepreneurs who participated in the training program aboard the ship in Mutsamudu, Comoros....