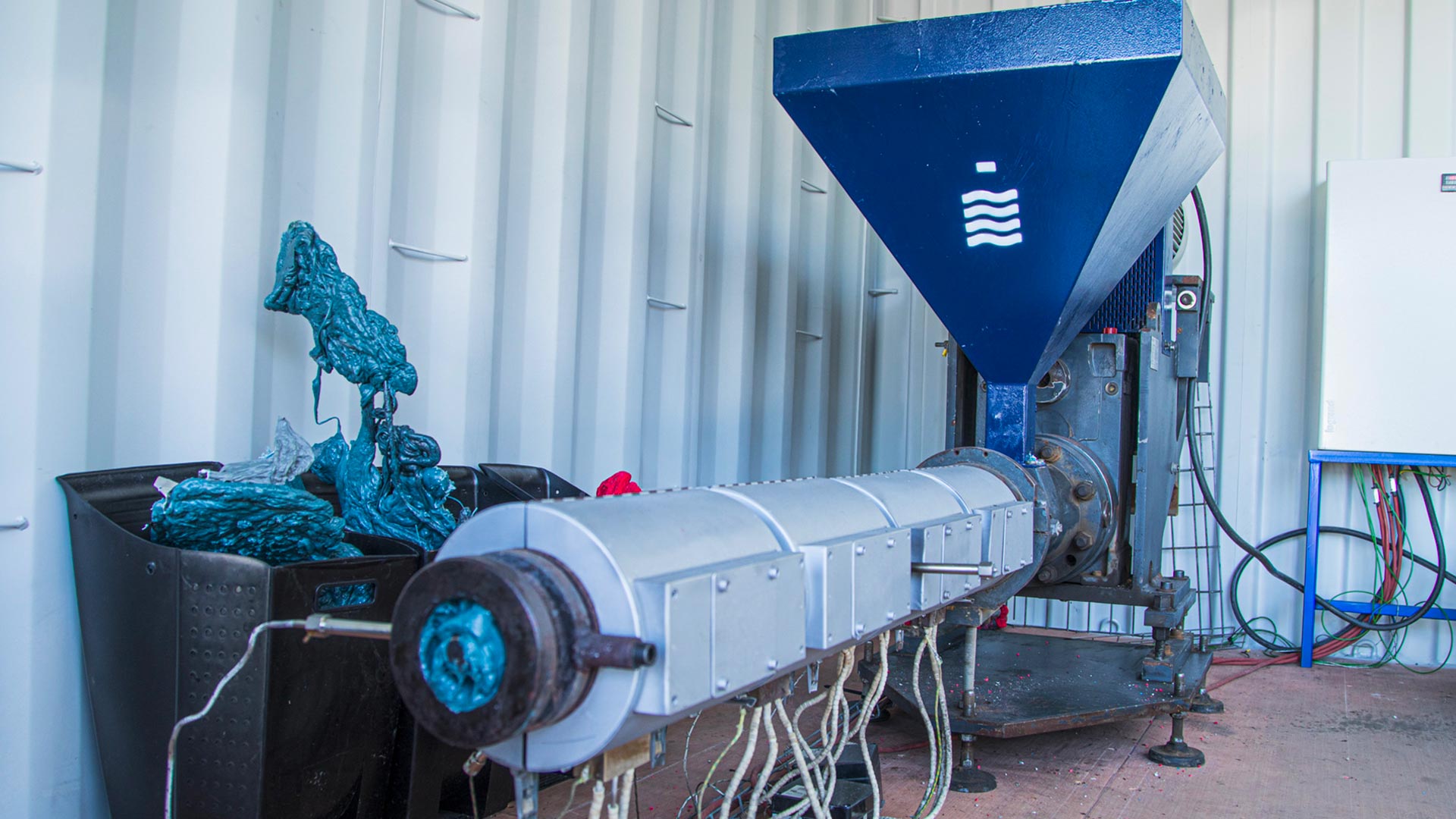
Presentation
Extrusion is a shaping process widely used in the plastic industry. It is the key process for mechanical recycling. Extrusion consists of gradually heating shredded plastic particles to form a soft, viscous paste later shaped to create new objects.
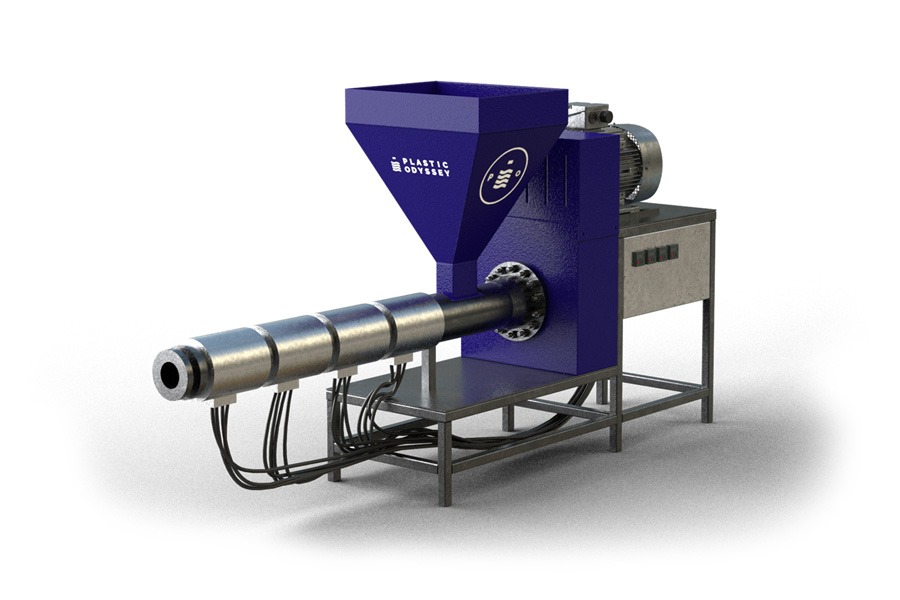
Items Description
An extruder is composed of four main elements, which include a motor that rotates and a worm screw inside a sheath heated by resistors.
Process Description
Once shredded, washed, and dried, plastic particles are placed in the hopper. They flow progressively into the sheath, heated by the surrounding warm resistors. A worm rotates in the sheath propelling the plastic to its end.
The plastic is gradually heated by the sheath’s warmth and its friction with the screw. The initially shredded plastic then becomes a homogeneous soft paste. At the end of the sheath, a die allows the molten plastic to flow out.
Entrance
Shredded PE – PP
Exit
Malleable Molten Plastic Paste
Case Study
Extrusion is rarely known on smaller scales, as the machine requires an initial investment that can be substantial, as well as a certain level of expertise concerning its process. However, it is an essential part of the recycling chain as it allows the shaping of previously developed plastic waste into new objects. Thus, it adds significant value to plastic waste.
The alternative to extrusion is to melt the plastics in a heated container, like a pan on the gas. The melting temperature cannot be regulated, so plastic tends to burn and emit noxious and polluting fumes.
Technical Information
Dimensions : 300 x 80 x 150 cm (length x width x height)
Weight: 1 500 kg
Electric power: 00 kw
Heating temperature: 150 – 250 °C
Approximate cost: 20 000€
Latest News
Local Factories: A New Plastic Waste Recycling Unit Installed in Mauritius
Plastic Odyssey, in partnership with Rogers Group, has inaugurated the first plastic recycling unit in Mauritius: a micro-factory capable of processin...
Hackathon with École Polytechnique de Thiès: Innovating for the Dakar 2026 Youth Olympic Games
As part of the “SUNU Plastic Odyssey” project supported by the French Embassy in Senegal, Plastic Odyssey and the Ecole Polytechnique de Thiès ha...
Local Factories: A New Plastic Waste Recycling Unit in Saint-Louis, Senegal
As part of the "SUNU Plastic Odyssey" project supported by the FEF (French Embassy Fund), Plastic Odyssey and BANCO have joined forces to deploy a rec...