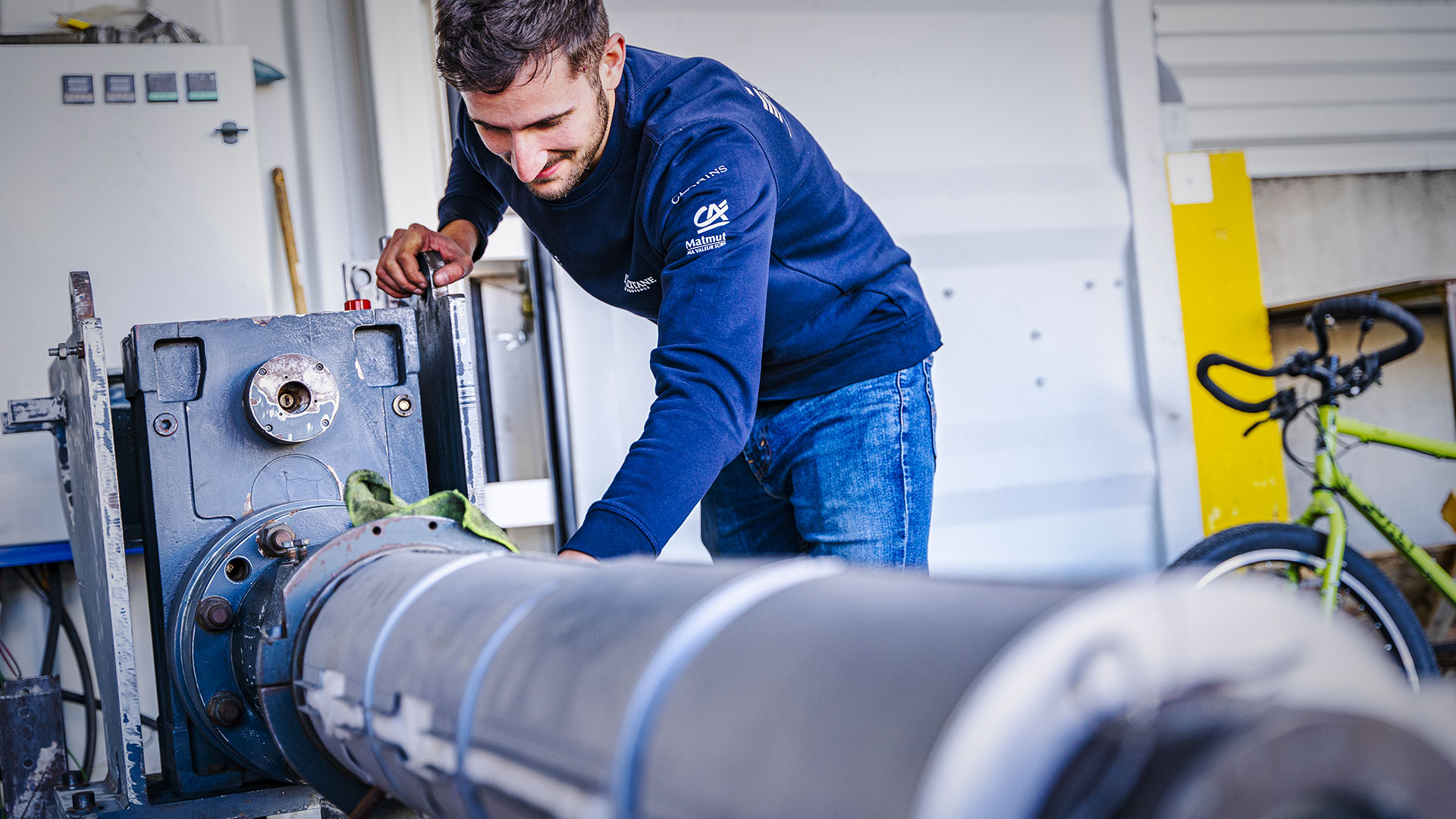
Article written by Tom BĂ©bien, Plastic Odyssey’s Recycling Workshop Manager.
The Role of Recycling Machines
The use of these machines on board will enable to carry out demonstrations to convince contractors of the stopovers’ countries to reproduce and install them ashore. Their role is simple: to demonstrate that plastic waste can be a valuable resource. Once collected and processed, plastic can be used for local purposes: building structures, irrigation for agriculture, designing flooring and furniture, etc.
This week, we are taking you behind the scenes of our plastic waste recycling workshop. From design to manufacturing, you will know everything about our technology development process.
Updated on Tuesday, March 16th, 2021
Simple, Adaptable, and Open-Source Machines
These machines have been conceived while taking into account three main criteria:
- The low-tech aspect: they are designed with basic materials easily accessible. They can be built and fixed with simple tools.
- Adaptation: the machines’ design is not unique. We started from an efficient basic principle, enabling the geometry, the scale, and the feeding to adapt according to the situation.
- Their design and manufacture are open-source: by developing our technologies, we have the hand over the entire construction process, and therefore know the parts down to the smallest detail. We can then disseminate and share all the elements and improve them in collaboration with local actors.
The Recycling Workshop’s Approach
The principle of our approach is to have the first set of efficient technologies to enable their development. We then target the unmanaged areas where plastic waste accumulates. Finally, we are working with local actors to adapt these machines to a defined use to give a second life to the existing waste on-site.
What is the plastic waste recycling workshop composed of?
Today we have a workshop that consists of three parts:
- The “material preparation” part includes a shredder, a washing tank, and a centrifuge to shred, wash and dry plastic waste.
- The “transformation” part allows us to re-form the material thanks to an extruder and molds of various sizes and shapes. This process can also take place thanks to an oven and a hydraulic press.
- The “energy recovery” part allows us, thanks to the pyrolysis unit, to recover non-recyclable plastics into fuel.
In total, we have ten machines: seven that we have designed and manufactured, one that we have recovered and adapted to our needs, and two others that we purchased (because very basic).
These machines are now being fine-tuned in Marseille to fit the vessel. They will then be sent to Dunkirk and taken onboard in April. Once installed, these machines will be able to get tested in appropriate conditions, which will officially launch the beginning of our expedition!
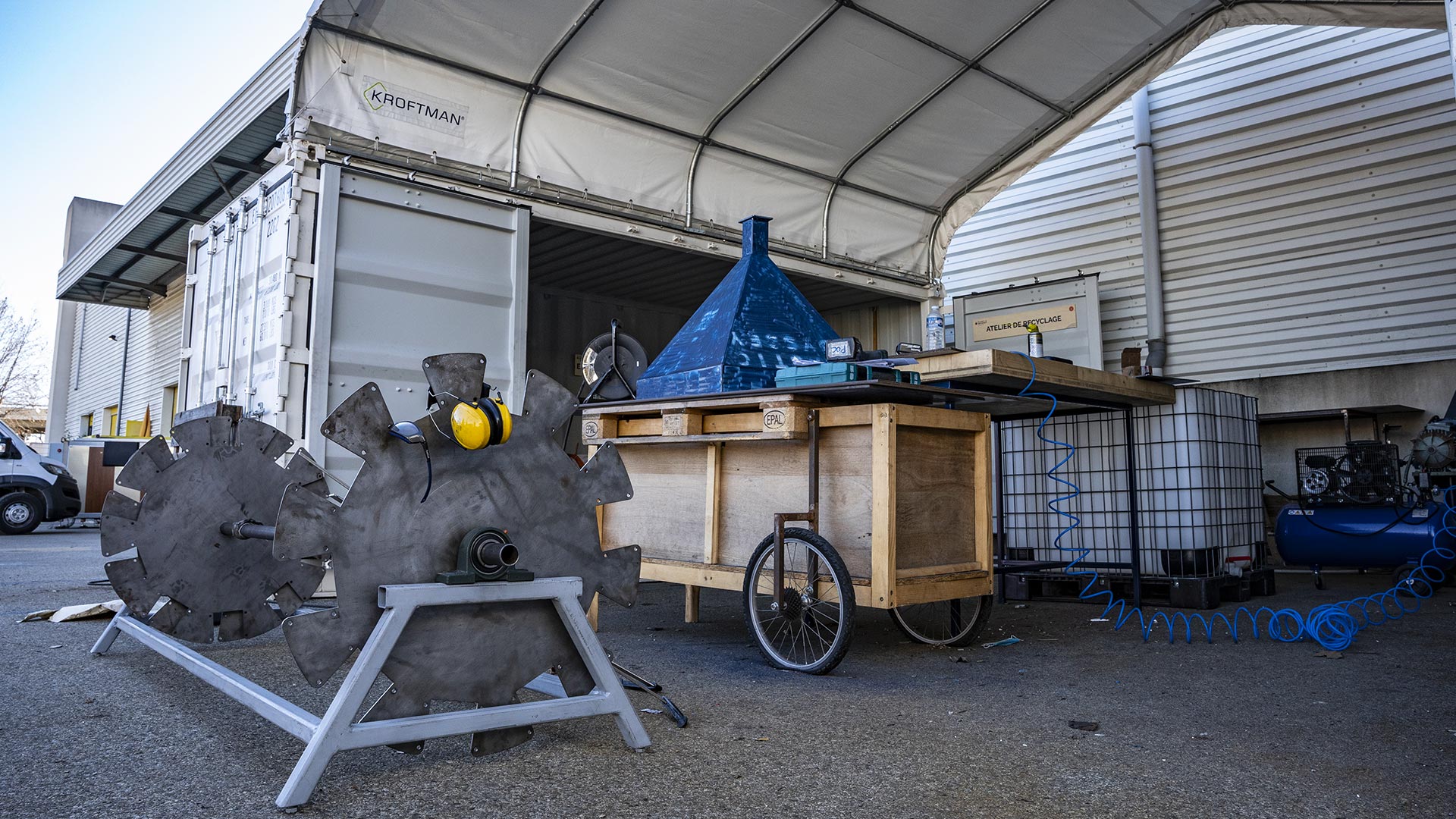
Updated Wednesday, March 17th, 2021
From blueprints to their installation on board, discover the story of the machines
I joined the project two years ago. Since then, I have been working daily on the recycling machines. And before we got recovery machines that fit our needs, we went through several steps!
Sources of Inspiration, Research, and Study Trips
The first step was to define which machines are essential in a basic plastic waste recovery process. So there was an initial phase of research into what is being done in the industry. We have visited several recycling centers in France mainly, but also in Germany and England. It gave us a good idea of the processes used. It also enabled us to fully grasp the complexity of recycling, each type of waste requiring a particular recycling process.
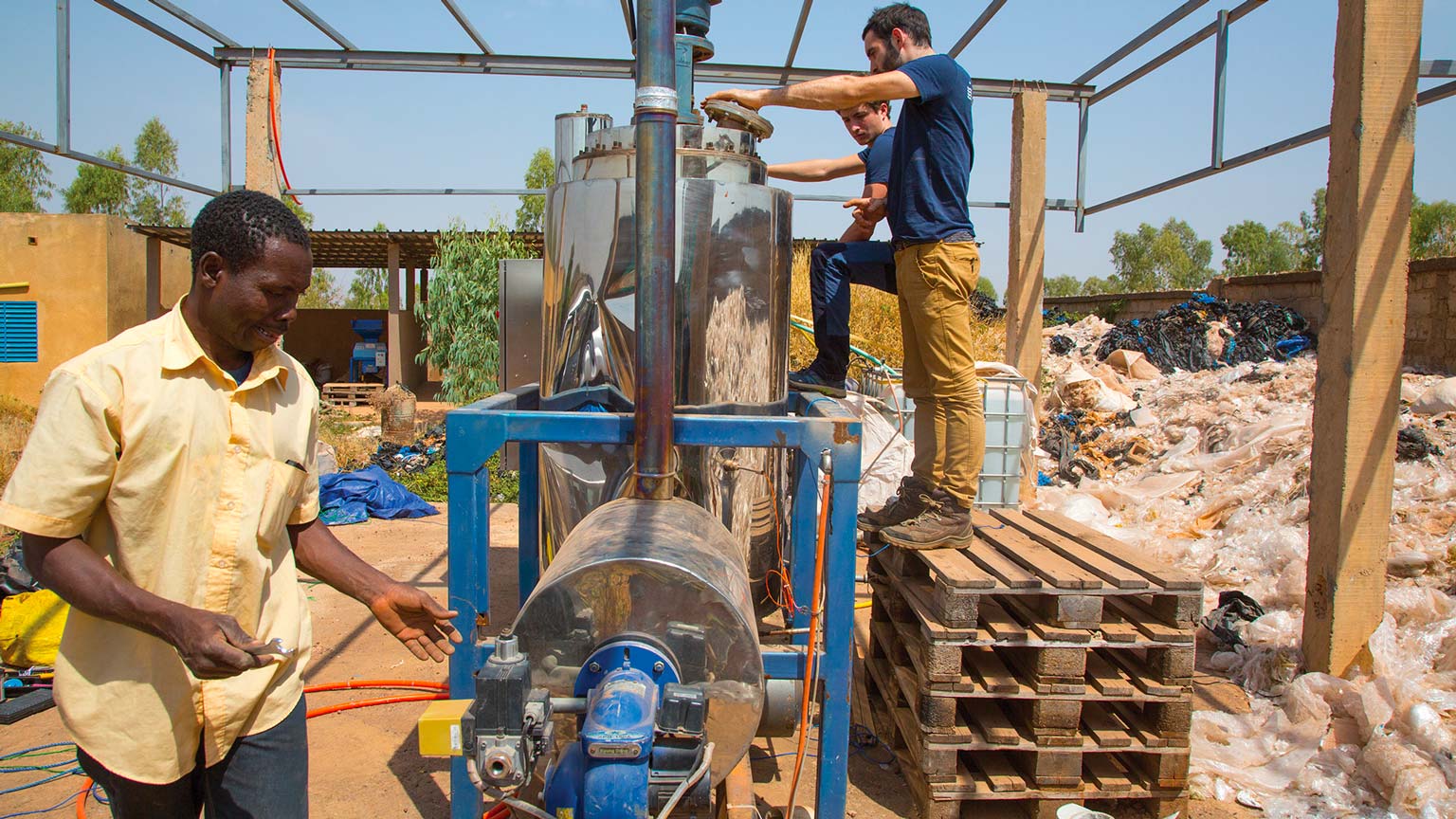
But mostly, we have come closer to what already exists in the field, on both a small scale and in informal contexts. We have contacted dozens of recycling project leaders in Africa, South America, and Asia. We had the chance to talk at length about their actions, what they use as processes, their feedback, and the definition of their needs. It was a rewarding experience, where we learned a lot about the different uses of these machines in the field. We understood that the machines themselves could be very different from the industrial machines we had seen in Europe.
Meeting with the Zabaleen Community in Egypt
The next step was to conduct study tours in Burkina Faso, Thailand, and Egypt. These study tours were very important for us, as we were able to meet actors of local ecosystems, attend demonstrations, and participate in concrete explanations.
In Egypt, for example, the Zabaleen community has been working informally in recycling for over 50 years. There are thousands of them every day collecting, sorting, and recycling the waste of Cairo. Their experience is truly impressive, as they build some of their own recycling machinery, including shredders and extruders. The shredders built in this community can be found in other regions of the world, where recycling is a work in progress. Notably, in Kinshasa, a plastic bag recycling project uses a shredder made in Cairo!
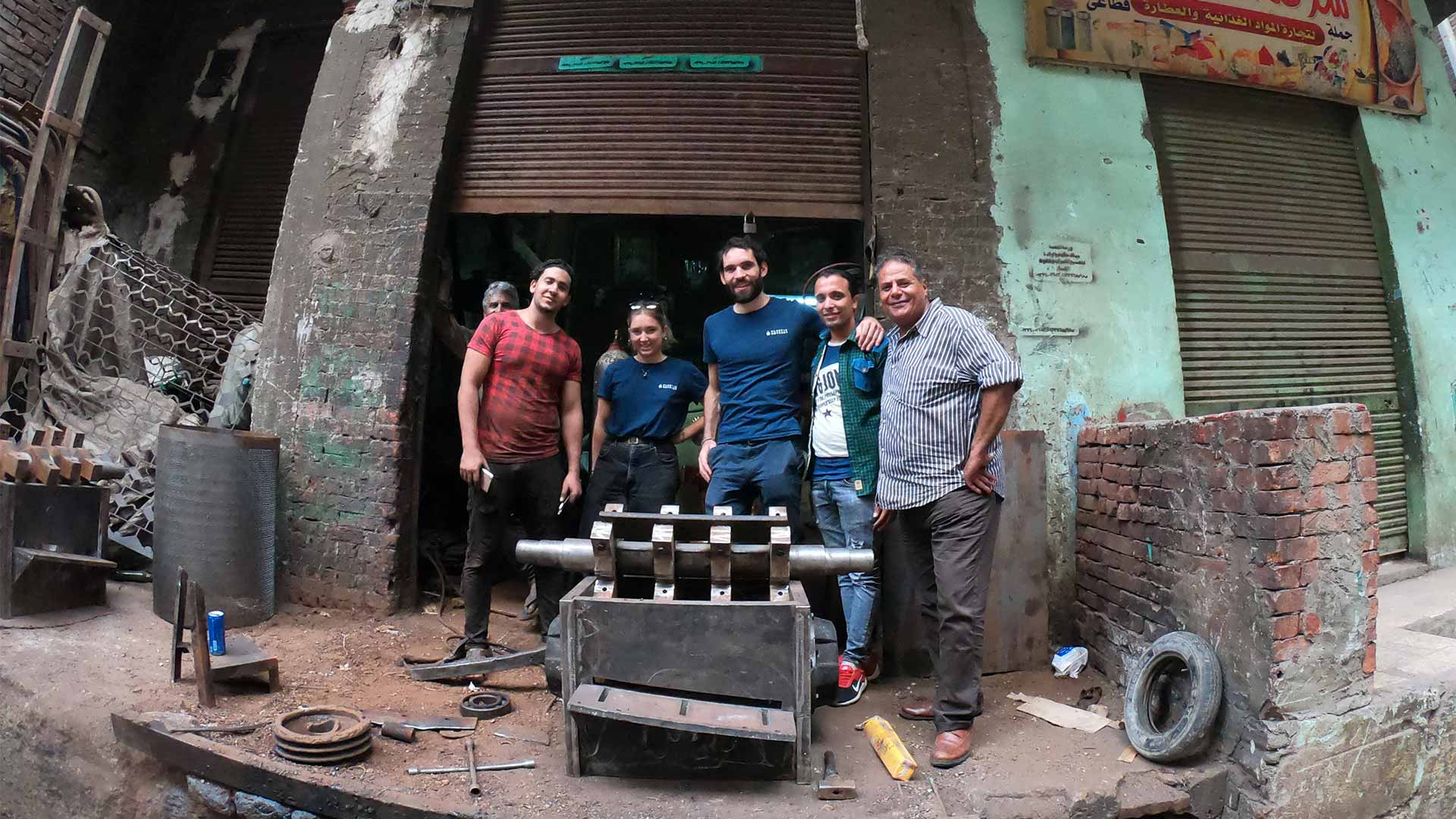
Thanks to this approach focused on research and field studies, several concrete examples of the application of our future recycling machines are taking shape. Also, these examples allow us to study the subject of quite varied types of waste.
Largely inspired by these examples, we can precisely identify the machines that we will embark, to meet our criteria of simplicity and robustness.
Design, Manufacturing, and Documentation
We made the design ourselves from what we had been able to study, with some improvements in terms of safety, and some adaptations necessary for boarding the Plastic Odyssey vessel. The design allowed us to document all the parts, create accurate drawings and realize the difficulties that could arise during manufacturing.

Our obsession in the design phase is to minimize the number of different materials to use in manufacturing. For example, the frame of our shredder was designed to be made out of a single type of steel bar, with a square cross-section. No part of the frame should be laser-cut. Whenever we can, we avoid custom-made.
The design process consists of defining the use of the machine, then finding technological means to meet this use. We have to choose the parts, size them, define the materials, check that it is strong enough for the use we have and think about how it will be manufactured and assembled. We are fortunate to have modeling software to draw the parts and verify that everything fits together correctly. In this way, we can save time and money as the alternative would be to make several prototypes in physics, then adapt them.
The Plastic Waste Shredder Example
Here is a 3-dimensions drawing of the shredder. This blueprint gives us a pretty good idea of what it will look like in reality. Once you have thought of everything, you can make each piece and assemble it.
There are undeniably surprises between 3D and reality, notably the volume that it takes up in space, the weight of each piece, etc. But if the design is well done and well thought out beforehand, surprises are rarely upsetting!
For every machine we have developed, we have gone through the following stages: design, modeling, and blueprinting.
Updated on Thursday, March 18th, 2021
The Manufacturing of Machines
The Arrangement of the Workshop in Marseille
Most of the machines were manufactured in our workshop in Marseille: a 50m² space in the warehouse of Lemon Tri – a social integration company that handles the sorting and collecting of waste in companies. We then had to equip the workshop with simple, yet essential tools, such as raw materials, and everything we needed to work on the manufacturing.
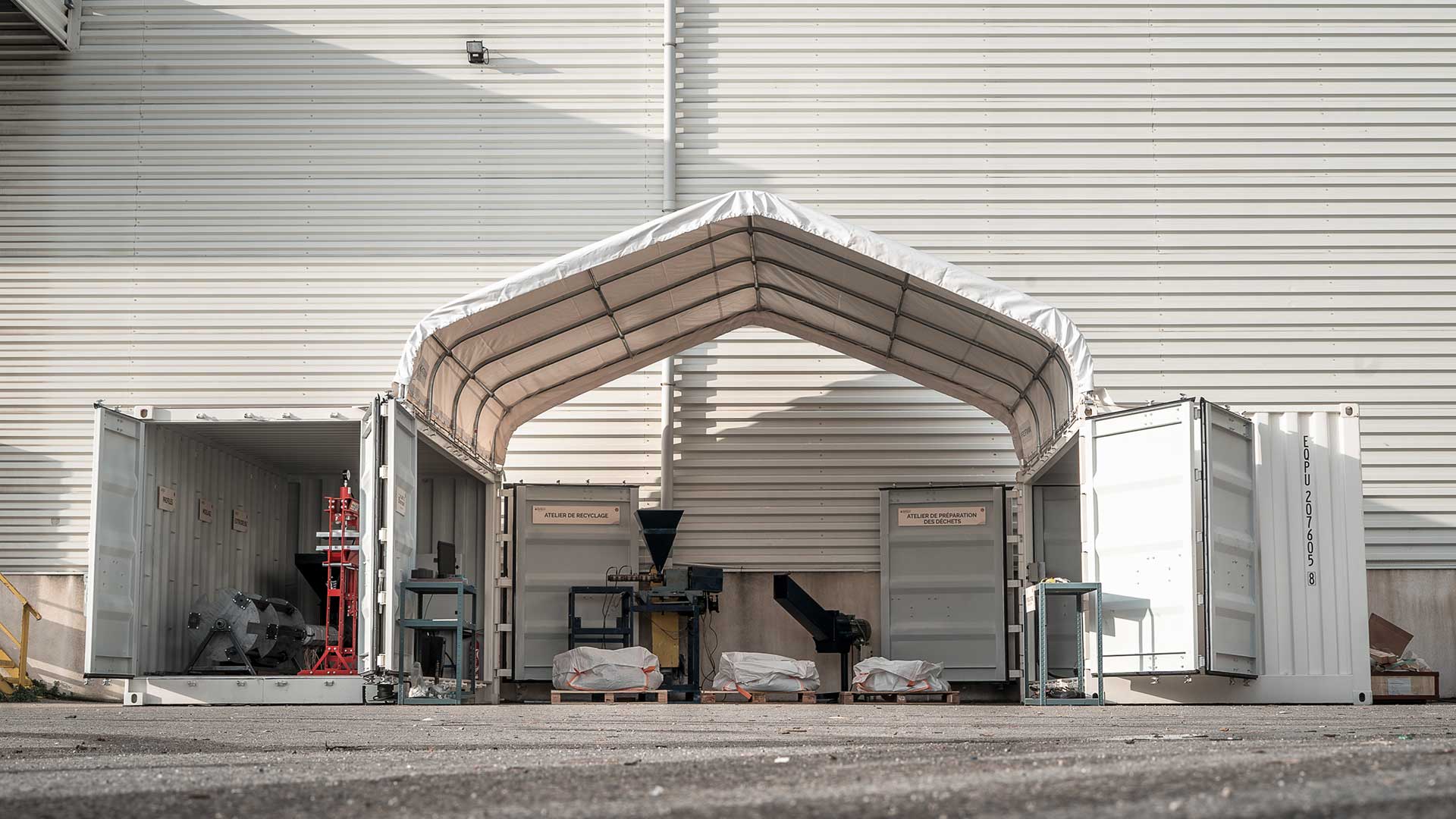
The Stages of Production
Following the design stages and after verification of the blueprints, we move on to manufacturing. This takes place in several stages:
The first step is to collect or order the raw material, the different parts composing the machines, and the specific elements like motors or bearings. We try as much as possible to reuse or recover elements. For the shredder, for example, we needed all the necessary steel profiles for its manufacture: the plates, the motor, the blades, the screws, etc. Once everything is gathered we cannot wait to start producing!
Each piece has then to be prepared one by one. From a 6-meter square steel profile, we have to cut it into several pieces to the desired dimensions.
Once all of the parts are ready, we start the assemblage by sub-assembly. The frame, the motor support, the hopper, the collecting tray, the axle, etc. All this with simple tools, a soldering station, and a lot of elbow grease!
We then proceed to the complete assemblage by linking all the sub-assemblies together. The machine is finally taking shape. This is how we can realize the volume and space it will take on board.
All that remains is to build the electrical cabinet and electrically wire the motor. In France, we are subject to strict protection standards. The electrical cabinets of the machines are simple. Yet, they contain necessary components for the protection of people and equipment.
Then comes the time for testing. A little apprehension, yet a lot of excitement, when the time comes to plug-in and start the set. No breakage, no injuries, it works, everything is fine!
Finally, a few adjustments need to be made, and everything can be disassembled to take each part or sub-assembly for painting. For our expedition, painting is essential to protect the machines from corrosion since they will be onboard the ship.
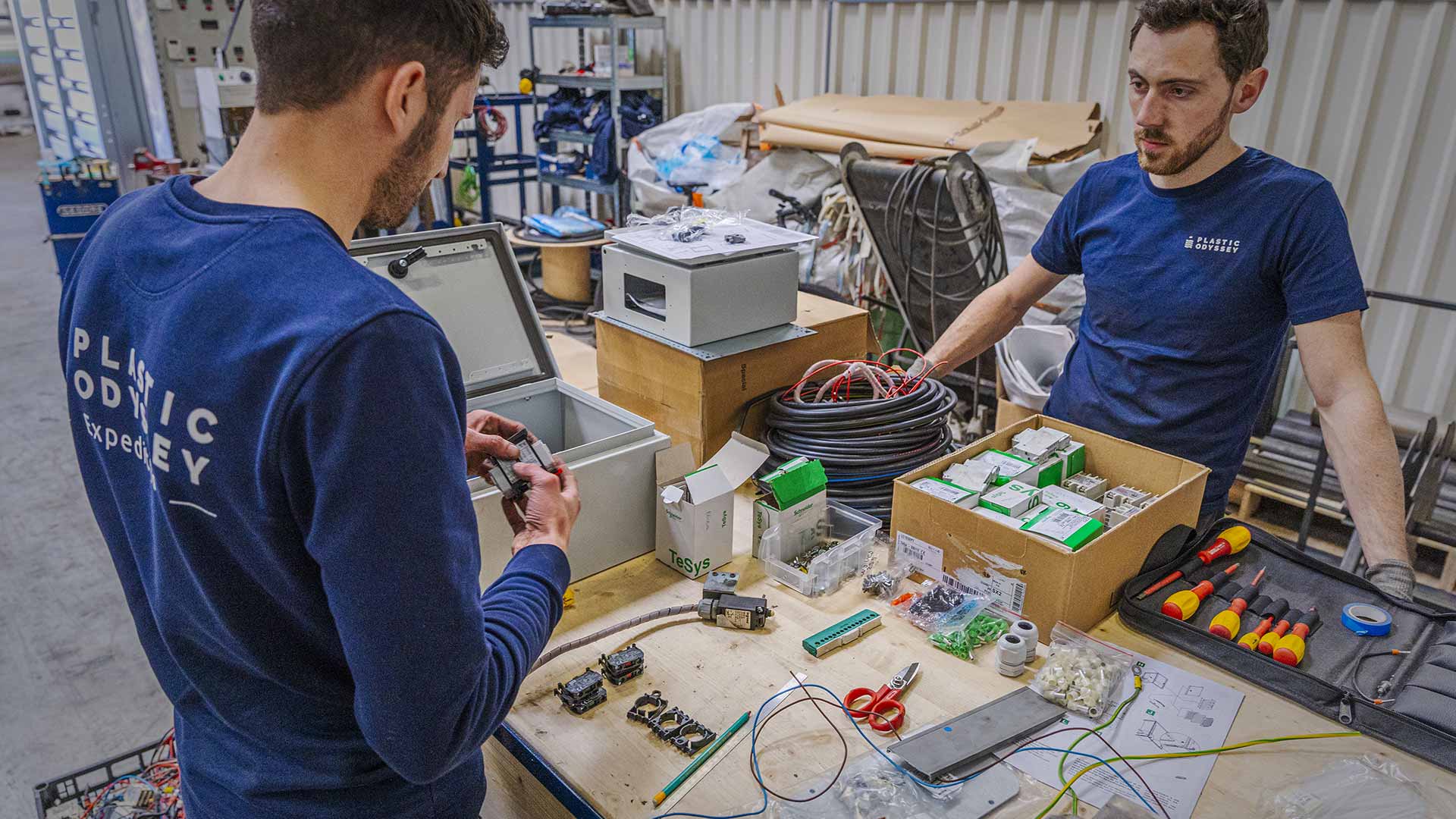
Cost and Production Time
In our workshop, we gave birth to the sorting table, the washing tank, the plate furnace, the barrel, and we repaired, modified, adapted, and tested the extruder.
The grinder and the centrifuge were made at the Cité des Arts de la Rue in Marseille, in the Sud-side workshops. Their expertise and the equipment at their disposal made it possible to manufacture these two machines in only two weeks!
Overall, all machines were manufactured in only two months. The manufacturing processes were quick and inexpensive compared to similar capabilities in the industry. Thanks to simple designs, basic and accessible tools, and the use of standard materials that can be found everywhere.
As an example, the expedition’s shredder, which has a power of 15 kW, cost us almost 12 000€ to manufacture in France. Approximately 5 000€ of materials and 7 000€ of labor, which represents 10 days of work for both machines. In the industry in France, a shredder of this capacity is around 30 000€ minimum.
Updated on Friday, March 19th, 2021
We’re almost there!
The vessel was put back afloat on March 9th, in the Plastic Odyssey colors, and the time has come to take on board all the machines that make up our recycling workshop.
This marks a big step and a lot of emotions for our technical team, noting the end of 2 years of hard work.
In a few weeks, follow the assembly of the recycling machines on the vessel. We will share this progress LIVE.
To end this article in beauty, here are some pictures of the assembly and manufacturing of our shredder.
Tom BĂ©bien, Plastic Odyssey’s Recycling Workshop Manager, is in charge of the design, manufacturing, and continuous improvement of the machines. He works with the technical team composed of Bob Vrignaud, co-founder of Plastic Odyssey and R&D Director, and Baptiste Lomenech, plasturgist technician. The development workshop is located in Marseille, and the machines will be sent to the Plastic Odyssey vessel in a few weeks.
Latest News
Tanzania: building a local recycling industry
Discover the plastic waste recycling entrepreneurs who participated in the training program aboard the ship in Das es Salaam, Tanzania....
The Global Plastics Treaty in Geneva: No Sleep, No Treaty
The UN Plastics Treaty is intended to become the first legally binding global agreement to end plastic pollution. Negotiations have taken place throug...
Comoros: An Archipelago In Search Of Sustainable Waste Solutions
Discover the plastic waste recycling entrepreneurs who participated in the training program aboard the ship in Mutsamudu, Comoros....